摘要 摘要:硬质材料像高合金化高速钢在磨削加工过程中出现的复杂热机械载荷,会影响表面完整性进而影响工程零件的性能。残留应力则是评估磨削零件性能的一个显著参数。早期研究指出磨削工艺通常就是...
作者:Haifa Sallen, Hedi Hamdi
摘要:硬质材料像高合金化高速钢在
磨削加工过程中出现的复杂热机械载荷,会影响表面完整性进而影响工程零件的性能。残留应力则是评估磨削零件性能的一个显著参数。早期研究指出磨削工艺通常就是工件的拉伸表面残余应力的来源。本研究中,通过x射线衍射对磨削工件的测量发现表面产生较大的压缩残余应力。为理解该残余应力的来源,实验建立了
外圆精磨有限元素模拟模型,且温度取决于材料属性;并采用SYSWELD 2010软件根据二维数值模拟建立了热机械模拟。利用工件表面移动的等量热通量来模拟CBN
砂轮对工件的加工作用。根据实验测量和分析计算求得热源轮廓。将砂轮的机械作用模拟为分布在接触区磨粒上的正常压力。求得温度分布和残余应力。模拟结果和测量结果之间的差别是比较明显的。进一步对磨削表面层进行表征,发现在给定的工艺参数、砂轮和材料属性条件下,等量载荷的热机械模型不足以在塑性变形和结构变化中再生诱导残余应力。
关键词:磨削,残余应力,有限元素模型(FEM),表面结构
1、引言
高合金化高速钢(HSS)由于其碳化物和马氏体基体的硬度非常高而被当作耐磨材料,并应用在钢材轧制等强力苛刻加工工艺的成形工序中。在加工前对这类机械零件的表面完整性进行一个预测可以保障加工过程的安全性和产品的质量。表面完整性的主要指标有表面微结构和残余应力等。本论文主要对
CBN砂轮对高速钢进行外圆精磨加工时所产生的残余应力进行研究分析。
有研究者指出残余应力轮廓主要受最后的制造加工影响,而制造工序也是影响最终表面完整性的主要因素。磨削作为一种精确加工工艺,适宜高硬度终极精磨材料的加工。对于光滑表面和精准公差要求高的零部件加工,磨削是其工艺的最后关键一步。但大多数加工操作中由于碎屑形成机制的缘故,很大一部分能量被转化为热能并在
磨料-工件之间产生高温;最终导致以表面软化为形式的热损伤、残余应力和再硬化。
在磨削工序中,砂轮类型、材料硬度和工艺参数等因素都会影响零件的应力状态。在砂轮类型方面,Kohli等人研究发现传统
刚玉砂轮加工时传递到工件上的磨削能总量约有60-75%被转化为磨削区的热能;而CBN砂轮的这一数据约20%;所以使用CBN砂轮能够降低热损伤。
为研究工件磨削过程中残余应力的来源及其形式,实验建立了FEA物理模拟。数值模拟需要对耦合现象的不同类型进行建模:热力的、机械的和冶金的。一些研究者提出了不同的建模,其中考虑了部分或所有的以上现象。在最为普遍的FE模型中,工件上的移动热源代表砂轮。因此,需要知道传导入工件的热通量密度。大多数温度模型都根据Jaeger理论求得磨削工件上的温度分布。但现有模型大多都忽略了砂轮的机械作用,在热源的结构影响方面有所局限。
本论文利用CBN砂轮对高速钢进行外圆磨削加工,从而研究残余应力分布及其变化。通过等量热源的耦合热机械FE模型求得模拟实验结果,将模拟结果与实验实测结果进行对比。对比差异主要表现为较高的压缩残余应力来源,特别是在低温和高热稳固材料(HSS)的条件下。然后,通过次表面微结构的详细分析做进一步的完善。
2、实验
2.1 实验磨削装置
本研究采用HERMLE CNC 5轴加工中心进行外圆外围纵向精磨加工;所用CBN砂轮直径Ds=150mm,宽度b=12mm;工件为硬钢柱,直径Dw=116mm、200mm,硬度为63HRC;设计定制特殊的喷嘴用于磨削区的油润滑。整个实验装置如图1所示。
图一:实验装置
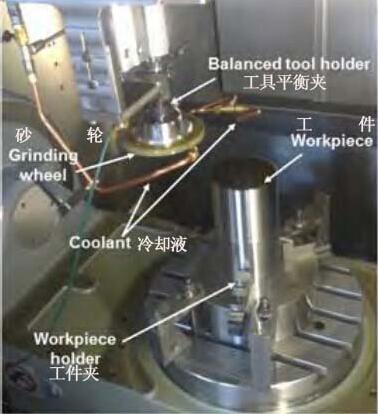
根据包含5个工艺参数和混合水准(两到三个[32 23])的部分析因试验设计进行实验,共计36组实验;加工方向为顺磨、逆磨两个方向;不同砂轮速度、工件速度、切割深度、进给速率和磨削防线。如表一所示。
表一:因子水准分配
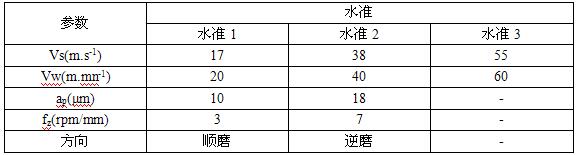
2.2 残余应力测量
每组实验做完后,利用带有铬放射线 Cr Kα(λ=0.229mm)和一个3.14mm直径的入射光束准直器的MGR40头的PROTO X射线衍射进行残余应力测量,如图2所示。对铁板(211)的测量也用该装置,Bragg’s角2θ=156.1°。以ψ正负值进行sin2ψ方法的测量:
6-ψ角度(-30°~+30°)
Ψ振荡:±3°
对表面层进行持续的电溶解直至达到要求的深度后就可以实现彻底的残余应力分布。以两个正交方向进行残余应力的测量:进给方向(σzz)和砂轮切削方向(σxx)。
图二:X射线机进行残余应力测量
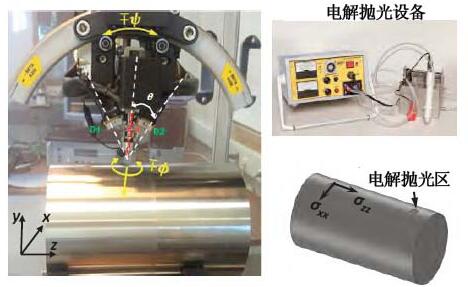
3、实验结果
图三为磨削加工前后工件的残余应力深度轮廓数据。由图观察可知,前期加工工艺所产生的拉伸表面残余应力在经过磨削加工后,被转化为最大表面压缩应力。
图三:HSS外圆磨削前后的残余应力
根据参考文献[20]对残余应力反映图中实验设计的分析可知,工件速度对磨削试样上产生的残余应力的影响最大,其次是砂轮进给速度。图4为顺磨方向上不同工件速度(7、14、22m.min-1)和经过修整的其他工艺参数条件(Vs=17m.s-1,fz=3mm.tr-1,ap=8μm)下求得的残余应力轮廓。在两个方向上,残余应力是完全压缩的。值得注意的是,位于外层的压缩峰值在Vw=7m.m-1处最高且主要在切削方向上(4a)。进一步分析则会发现,峰值之间的差异更显著,工件速度对残余应力的影响表现在了磨削表面下方的受影响层上。工件速度越低,受影响深度就越大,从Vw=22m.min-1的10μm到Vw=7m.min-1的80μm。
图四:不同工件速度条件下的残余应力轮廓
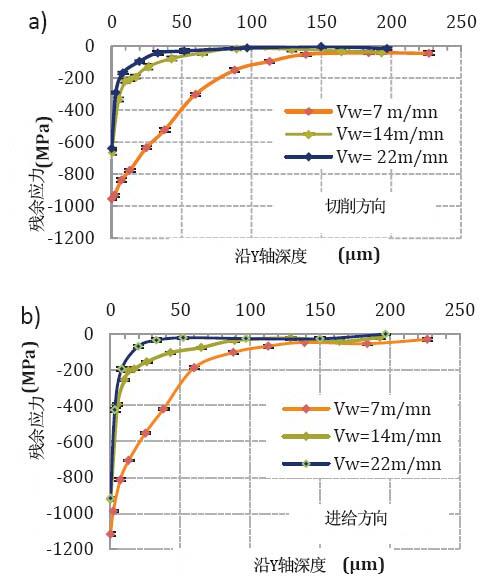
4、外援磨削加工后残余应力的计算模型
4.1 数字模型设计
数字模型主要用来模拟外圆精磨工艺中产生的残余应力,如图5所示。所采用的方法并未考虑切屑去除机理。将砂轮假设为随着工件速度Vw沿着表面移动的热源。
图五:数字模型:热载荷和界面状况
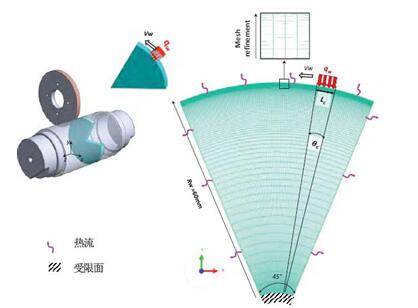
在砂轮的单圈加工过程中,沿表面的磨削条件在切削、进给两个方向上保持常量,因此可以仅考虑柱工件的一部分即可。利用SYSWELD软件对柱件的第8个2D平面应变模型进行处理。在建立该2D模型时还要考虑不同温度条件下的材料属性。
工件的初始温度T(t=0)=20℃。在上表面和侧面,用热对流传导系数hconv(W.K-1.mm-2)来表示热对流。底面的热损失假定为0。热边界条件如图五所示。
4.2 热源求值
热源长度和砂轮-工件之间的接触长度相等。
进入工件的热通量计算如下:
图六:热源计算
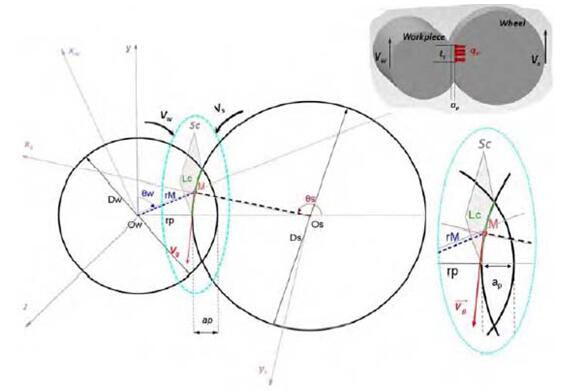
公式1为磨削过程中产生的总能量。Ft为磨削切向力,Vg为工件-砂轮滑动速度。此外,还观察到在磨削中所有产生的能量都被转化为热能。砂轮-工件间的热通量总量qT(W.mm-2)和公式4的滑动速度以及公式2中单位接触面积ft(N.mm-2)上的切向磨削力成比例关系。
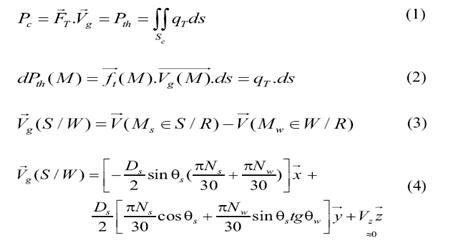
.
最后,工件qw(W/mm-2)上的热通量密度计算如下: 其中, εw是转化为工件上热量的总能量的一部分。在CBN砂轮配用油润滑加工中,εw约为20%。实验发现在外圆精磨中,热通量形状为准矩形。
4.3 机械模型装置
机械计算考虑了热弹塑性机械性能;求得弱耦合热机械计算。砂轮的影响模拟为速度为Vw沿着表面移动的正常压力。外加荷载的量级由接触区的正常磨削力求得。通过X、Y方向上对位移的限制求得工件底面上的运动学边界条件。
4.4 热学结果
图七为模拟的热学结果,条件参数为:Vw=7m.mn-1,Vs=17m.s-1,fz=3mm.tr-1,ap=8μm。
图七:不同深度条件下沿切削方向的温度轮廓
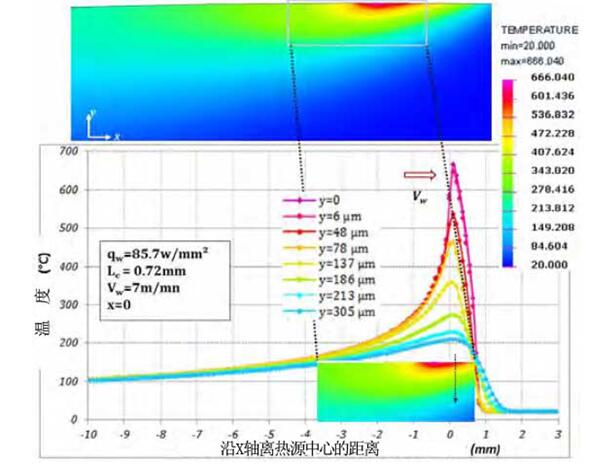
观察发现最高峰值温度接近Ac1=750℃(奥氏体化初始温度)。但达到一定深度后,温度超过了HSS(450-600℃)的回火温度。此外,由于冷却速率过高,磨削表面出现了高度集中的热梯度(≈300μm)。
图8给出了Jaeger分析策略对比,结果显示一致性良好;从而证实了数字模型。图中的差异主要是由于FE模型的热对流引起的热交换所致,而Jaeger模型则没有考虑该因素。
图八:不同深度条件下数值模拟温度和分析计算温度
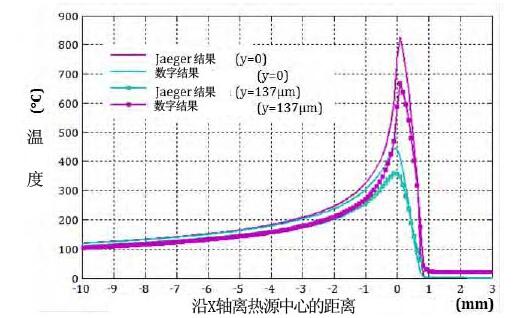
工件速度变化的影响如图9所示。
图九:Vw对磨削表面下的温度轮廓的影响
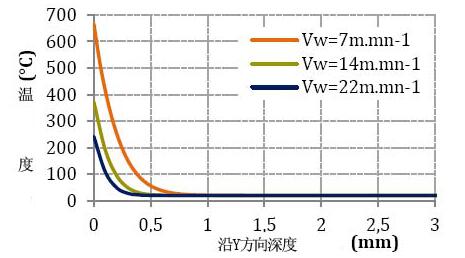
表面温度和热影响深度都达到最大,随工件速度的降低而快速增大。较高的速度缩短了接触时间从而降低了工件上的热量。
4.5 预测残余应力
图10为沿深度的计算残余应力轮廓(考虑、未考虑砂轮的机械作用),工件速度为Vw=7m.min-1(Tmax=666℃)和Vw=22m.min-1(Tmax=242℃)模拟值和实测值之间的差异是十分显著的。和实验测量相比,数值模拟的结果表明工件速度对残余应力有非常显著的影响。在较低速度下,切削和进给两个方向上都观察到了较高的表面拉伸残余应力。距离表面100μm距离时,该值逐渐降低至-100MPa(10a)。在较高速度下,磨削表面下观察到较低的压缩残余应力。值得注意的是,在所有加工中,砂轮的模拟机械作用对残余应力的分布无影响。
图十:残余应力轮廓(a)Vw=7m.min-1(b)Vw=22m.min-1
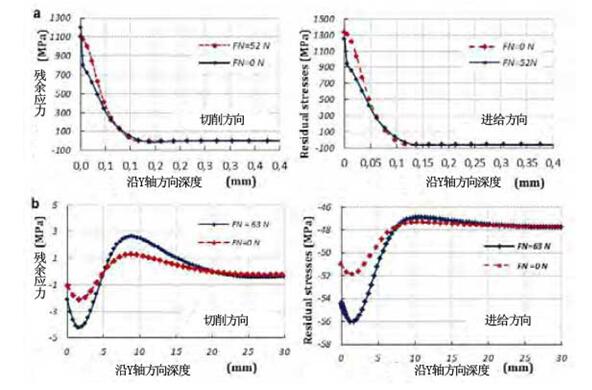
5、讨论
实验结果和模拟结果之间的显著差异说明了高速钢磨削加工中残余应力来源的很多问题。利用热机械模型求得的数字结果给出了两种残余应力状态类型:当热效应明显时(Vw=7m.min-1),拉伸残余应力产生,如图10a;当机械效应大于热效应时,产生低压缩残余应力,如图10b。本研究所用数字模型并未考虑相位变换引起的形变和材料回火以及工件上材料的脱落。所有这些现象都会降低拉伸残余应力并提高压缩残余应力。
由于冶金材料属性的信息缺失,研究重点主要集中在受影响层面上。磨削加工后,表面试样被涂附上一层树脂,然后进行机械
抛光和蚀刻。图11为改性层面,厚度约5μm。
图十一:HSS磨削表面微结构的SEM观察图
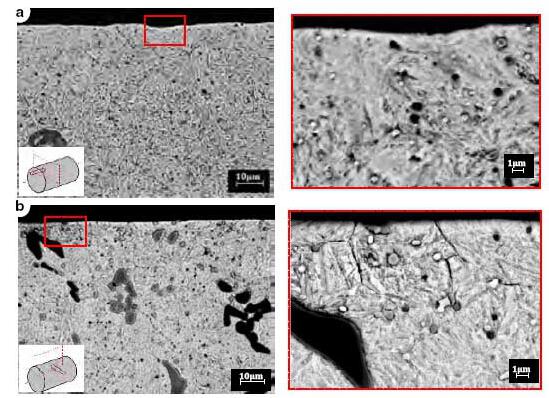
在图11a中,改性形成的层面可能是由严重的塑性变形引起的,也可能是由热激化奥氏体相变引起。磨削表面的压缩残余应力也可能是由磨削过程中经转化的残留奥氏体含量所致,如图11b所示。
此外,临近磨削表面的EBSD检测显示出较低的指数(黑色区域),这说明有其他相的存在,其变形的微结构和马氏体结构是不一样的。
图12:HSS磨削表面微结构的EBSD观察
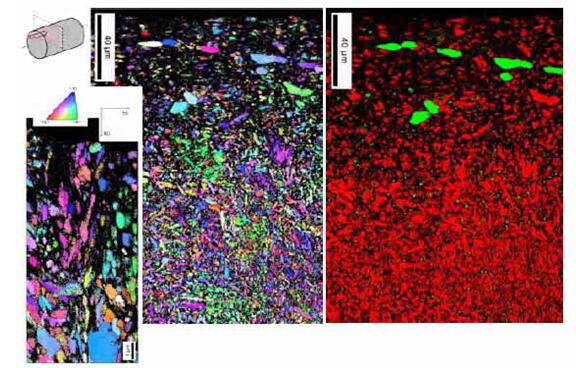
为更多了解改性层的相组份,实验还进行了磨削前后X射线衍射相分析。结果显示磨削和未磨削试样的马氏体相的观察图是一样的。
6、结论
利用CBN砂轮对高合金化高速钢进行外圆精磨加工后,表面层产生了100μm厚的显著压缩残余应力。实验测量显示工件速度是外圆磨削过程中最关键的动力参数,它会影响磨削试样上残余应力的分布。利用热机械模型求得的热学结果显示温度可以大于材料的回火温度并接近Ac1值。但数值模拟求得的残余应力和试验实测值并不匹配。磨削高速钢微结构的分析说明残余应力是机械、热学和变形效应共同作用的结果。变形结构的改性表面层有SEM/EBSD图可以看出。微结构的变化和磨削过程中残留的奥氏体相变、回火现象和塑性变形有关。(编译:中国超硬材料网)