摘要 作者:一级专家、研究员级高工刘随建航空发动机叶轮叶片加工难点航空发动机、燃气轮机叶轮(整体叶盘)、叶片加工难点与其叶型形状结构及加工质量要求特点直接相关,叶型在整体上具有的不规则三...
作者:一级专家、研究员级高工刘随建
航空发动机叶轮叶片加工难点航空发动机、燃气轮机叶轮(整体叶盘)、叶片加工难点与其叶型形状结构及加工质量要求特点直接相关,叶型在整体上具有的不规则三维空间曲面形式,使得其加工方式上构成了专业性质,而其同时具有的薄壁形式,又成为曲面结构精度要求达到始终不能避免的影响因素,叶型表面质量近乎苛刻的要求,也是成型精度保证在加工方式选择上必须考虑的问题。
由于叶轮(整体叶盘)、叶片的叶型是对航空发动机、燃气轮机中的高温高压的气体介质实施作用,受到离心、气体冲刷与复合振动等性质的交变应力作用,使得其材料性质必须具有轻质、高强度、高耐疲劳性能及耐腐蚀等综合性能,为此,零件材料就呈现了复杂的难加工性质,从而加剧了其加工的更大难度。为了实现叶轮(整体叶盘)、叶片高质量与高效的加工需求,其加工技术具有多专业、多种形式及持续性的创新发展,以适应产品结构与材料改变所富裕功能不断提高所具有的需求。
多轴联动加工中心设备对叶片制造技术发展的促进
1. 叶片型面净成型制造技术的发展
叶片制造传统的高效加工技术发展,主要是体现在叶型的净成型方面,即降低或完全去除叶型机械加工切削量(其中包含很多的手工钳修打磨操作)的方式来实现加工效率的提升,其中具有代表性的技术是精锻、辊轧与精铸技术(见图1)。
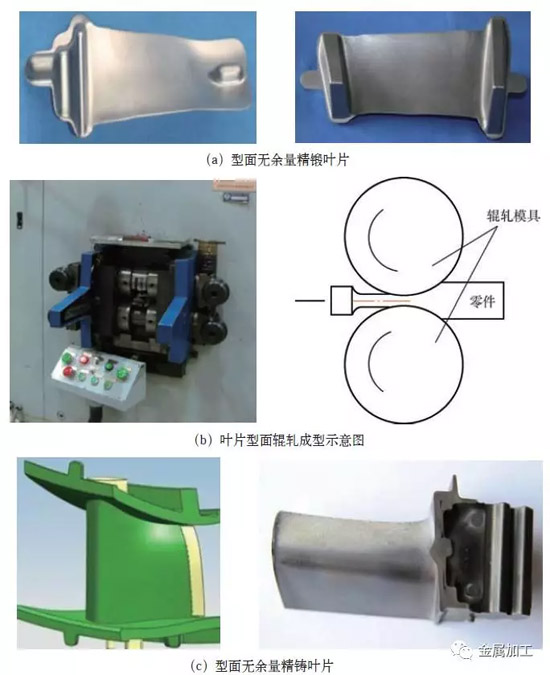
图 1
目前,随着电加工、机械加工等的多轴联动数控加工技术发展,以及机械手等先进加工技术的日新月异,使得模具加工精度水平实现与热加工相关流程中影响因素获得了较好控制,从而使叶片叶型的净成型加工获得很好的提高发展;并且由于多轴联动数控铣削、磨削加工的发展,使得利用精锻与辊轧形成叶型的进排气边补充加工,也由原来的手工打磨方式改变为机械控制加工方式,加工质量与效率水平也得到了促进提高,使传统的高效加工技术获得了新的促进发展。
2. 叶片加工快速反应能力提升技术发展
由于多轴联动数控切磨削加工技术的发展,使得叶片制造适应新机研制需求的快速反应能力获得了非常大的提升。传统的叶片加工工艺,因为叶片结构上的不规则形状,加工数量的成批性质,以及设备功能的局限性,使得叶片的缘板、榫头及型面等部位必须单独进行加工,加工工艺呈现很大的分散性,专用工装多,工序长,周转多,效率低。该种加工方式对于新机研制而言所存在的弊端尤其难以令人接受,主要体现是生产准备时间长,工序加工调试时间占比大,周转与加工时间比例不协调,完全不能满足新机研制所需的快速反应要求。
随着功能强大的多轴联动数控加工中心设备的出现,叶片加工工艺的改变具有了非常良好的基础。目前新机叶片研制的高效加工方式是,通过叶片两端工艺凸台的施加,使叶片能够实现一次装夹完成缘板、榫头和型面几乎全部位置的集成化加工,其专用工装数量减少可达90%,加工周转占比时间缩短可达80%,极大地提高了研制的快速反应能力。比较典型的两种集成化加工工艺方式如图2、图3所示。
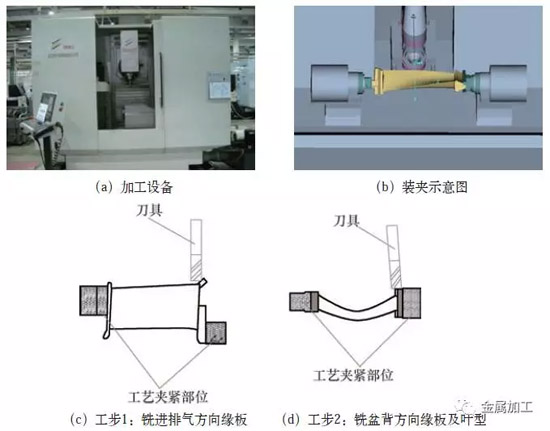
图2 叶片数控五坐标铣削加工中心设备集成化加工示意图

图3 涡轮叶片数控磨削集成加工示意图
发动机整体叶盘结构(见图4)的出现,很大层面的因素是由于多轴联动数控加工设备与编程软件控制技术的发展,尽管整体叶盘的粗加工开槽方式先后出现了水切割、电火花铣削等方式(见图5),但是由于整体叶盘、叶片之间流道所呈现的非线性且狭窄空间的特点,使得叶片型面几何精度的最终保证,仍然主要依靠于多轴联动数控加工中心设备的功能作用。
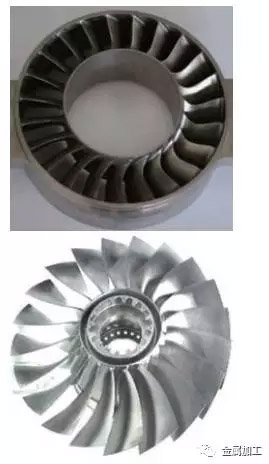
图4 开闭式整体叶盘示意图
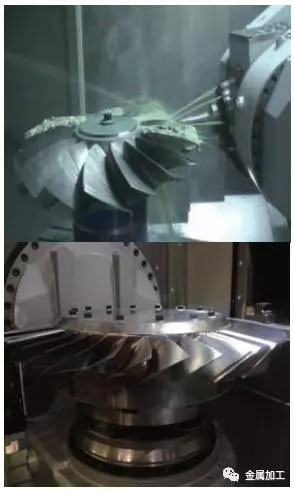
图5 整体叶盘数控加工示意图
特种加工工艺对叶片加工技术发展的促进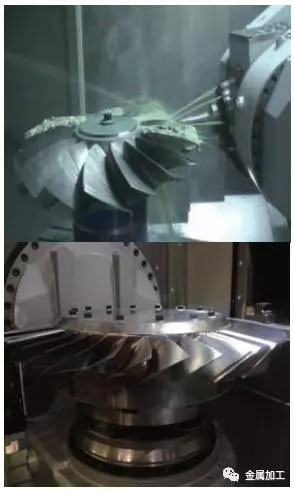
图5 整体叶盘数控加工示意图
1. 叶片型面精密振动电解
加工技术发展叶片型面的多轴联动加工方式尽管能够实现较好的快速反应能力,但其刀具的加工成本是非常大的,尤其对于高温合金一类的难加工材料而言,刀具损耗量几乎可以占到成本的30%~40%,并且型面的成型加工是走刀轨迹的集成,加工效率的提升空间有很大的局限性。
而叶片型面精锻、辊轧的净成型加工技术,存在着加工变形、加工精度保证难度大的问题,并且该两种方式还存在进排气边圆弧部分需要补加工的问题,补加工部分与已有型面部分的交接完好程度保证难度也比较大。
目前,新型的振动电解加工设备的出现,改变了型面加工精度保证、成本降低与效率提升之间的矛盾,其加工精度可达到0.02mm左右水平,由于加工是利用电极的全型面复映方式,叶片盆背两侧加工可以两端同时进给加工,效率水平高,并且理论上而言电极是不磨损的,因此,成本上也较低,但是对于叶片型面精度的达到,应该是有一定难度的,需要对电解液、电解参数及电极精度等因素的匹配控制,对于大批量叶片加工具有优势。以多轴联动数控加工中心设备与精密电解加工设备所形成批量生产工艺,具有加工精度质量得到可靠保证,并且具有高效率、低成本的特点,是叶片制造走向高质、高效加工的有效途径。
2. 叶片超塑成型加工技术
发展目前先进航空发动机风扇转子叶片普遍采用小展弦比的宽弦叶片,其主要目的是增大单级叶片的气动效率,同时解决振动与抗外来物打伤的能力,但是如果该种叶片采用传统的制造方式则存在质量大大增加的问题,发动机轮盘难以承受大质量叶片旋转后形成的强大离心力。
为了解决相关问题,目前的做法是将叶片做成空心或使用复合材料进行制造,采用钛合金进行制造的一种技术是,叶盆和叶背为两个分体的板片结构,利用材料的超塑性能使用模具进行成型,在成型的同时采用新型的扩散连接焊接技术将分体结构联结为一个整体叶片,中部空心部分采用蜂窝夹芯进行刚性加强,如图6所示。
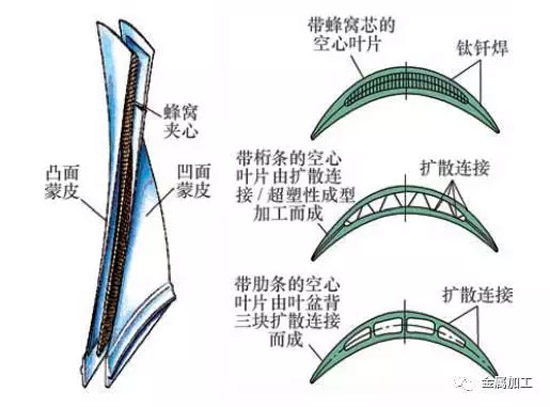
图 6
3. 双性能整体叶盘制造技术
目前压气机部分的整体叶盘基本是盘体和叶片采用同种金属材料,其制造基本是采用一个盘件的锻件通过最终加工成形。
而涡轮部分的整体叶盘则根据盘体和叶片工作环境差异,而采用不同的材料进行制造,比较典型的是由高温合金粉末盘与单晶高温合金叶片复合成形为整体叶盘。在制造工艺上,高温合金粉末盘与叶片分别采用热等静压法和铸造完成坯料制造,然后经过机加工分别完成各自成形加工,最后采用以下之一的方式完成双性能的整体叶盘制造,分别是:电子束焊接法、扩散连接法、线性摩擦焊接法及锻接法等,其使发动机的功能实现几乎达到了极致完美状态。
4. 叶片3D打印净成型加工技术
3D打印对于复杂的叶片坯料制造工艺改变具有非常大的意义,利用激光熔化烧结钛合金、高温合金粉末材料进行的叶片坯料制造,改变了传统锻、铸造工艺需要进行模具制造,多道次的加热锻打,或进行蜡型压制、型壳制造及浇铸等的众多工艺环节,大大简化了制造流程,并且具有较迅速的快速制造能力。
目前3D打印技术进行的叶片坯料制造,具有型面或空心内腔表面实现净成型,其他表面余量精确控制的状态。然而,产品制造所需的粉末材料性能保证、坯料冶金缺陷质量控制、热处理等技术满足使用要求的程度,仍然是制约工程化应用的重点研究环节。但是随着研究工作的不断进行,3D打印的叶片制造技术正在不断完善,其应用已经越来越接近于成熟。
结 语
叶片与叶轮是发动机和燃气轮机气动性能与效率功能实现的直接作用部件,其非常大地决定了发动机和燃气轮机的功能性质,多年来其材料技术、结构技术改变从来没有停止过。
伴随着零件材料与结构的创新性发展,其制造技术也呈现了多学科与多个领域的技术复合,其中包含着成型的实现,也包含加工效率、成本等综合效益方面的需求,无论哪一个方面技术的突破,都能够推动产品专业的进步,进而极大地影响发动机和燃气轮机整体制造技术的进步。
我们相信,只要发动机和燃气轮机原理功能不发生变化,叶片与叶轮制造技术的发展与进步则仍然不会停止,进而继续极大地影响发动机和燃气轮机技术的发展与进步。