背景介绍
某生产自然吸气发动机的客户,近期在磨削车间的法兰端磨削工艺中,出现了严重的粗糙度超差的情况,圣戈班磨料磨具应用工程师到现场进行技术支持。
曲轴是发动机中最重要的部件,它将连杆传来的活塞上下运动的力转变为转矩输出并驱动发动机上其他附件工作。曲轴受到旋转质量的离心力、周期变化的气体惯性力和往复惯性力的共同作用,使曲轴承受弯曲扭转的载荷,要求曲轴有足够的强度和刚度,其轴颈表面需耐磨、均匀、平衡性好,相应的,对于轴颈表面圆度,粗糙度,直线度和凹凸度等指标要求较高。
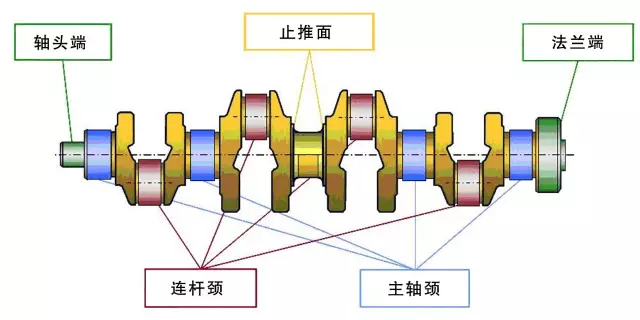
曲轴法兰端磨削部位
工件:曲轴
磨削位置:法兰端
工件材质:铸铁,HRC52-56
磨削余量 (单边):0.3mm
圆度要求:0.0035
粗糙度要求:端面外圆
修整参数: 修整量 0.02mm*2,走刀速度80mm/min
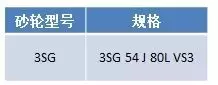
跟踪4个完整修整循环加工,抽检第1,3,5,7工件;
抽检工件圆度不达标,为0.007mm左右;
在一个修整周期内,抽检工件粗糙度,工件粗糙度Ra值从首件到末件呈大幅度减少趋势,从Ra 1.53降至Ra0.83;
抽检工件砂带抛光前表面无异样,砂带抛光后出现明显磨痕,所有磨痕出现在工件上相同位置。
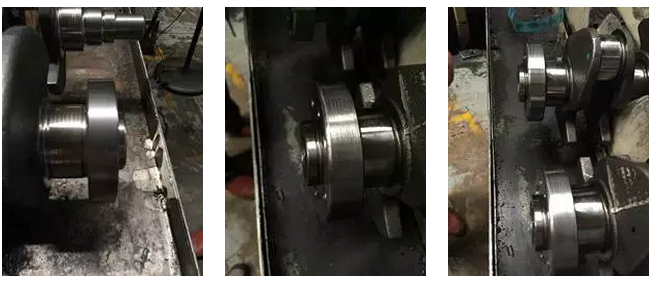
理论上,在磨削工艺中,出现磨后粗糙度超差,一般有如下几种情况:
砂轮本身粒度偏粗,测试工件表面相比正常产品光洁度较差,严重情况下会出现划痕;
砂轮硬度偏软,异常脱粒进入磨削区域,在工件表面产生随机划痕,影响工件表面粗糙度;
磨削系统滤过装置不好,导致磨屑或者磨粒重新进入磨削区域,形成随机划痕;
砂轮线速度过低,无法在工件表面形成有效切削,也会影响工件表面粗糙度,严重情况下也会出现规律性划痕;
修整工具:修整工具(主要是金刚石滚轮或者固定式修整器)的质量较差,修整过程中异常崩粒或者磨损,容易在砂轮表面形成相应高低点,造成工件表面规律性的划痕;
修整参数:重叠比设置过低(导程过高,滚轮与砂轮速比不合适,修整量过大等)。
在该客户曲轴外圆磨中,使用的是54粒度的砂轮,理论上工件表面粗糙度一般都达到Ra0.8以下。而首件工件Ra1.53,与理论值相差甚远;
通过与客户现场工艺工程师沟通,该工位上之前使用的砂轮已经调整过硬度,但是无明显改善;现场提升砂轮线速度(提升5m/s, 提升10m/s),首件工件粗糙度也并无明显改善;降低最后一道精磨进给速度,无明显改善;
降低修整走刀速度低至50mm/min, 修整后首件工件粗糙度改善至Ra1.39, 但仍然偏离实际要求值较远,且后续砂轮抛光后磨痕依然存在。
基于以上的工艺调整和信息汇总,我们可以总结出该客户工件磨后粗糙度严重超差的几个特点:
工件表面出现固定磨痕
粗糙度远远偏于理论值
砂轮本身粒度和硬度无明显问题
修整参数及磨削参数的调整只能带来轻微改善
所有这些特点表明:
修整后首件工件粗糙度严重超差与修整器本身有直接关系。
砂轮表面宽度方向出现了规律性的高点,这些高点在修整后出现,因此造成修整后第一个工件粗糙度远远偏离理论值和工艺要求值,而随着磨削的不断进行,磨料磨损后粗糙度得以改善。
通过与客户的进一步讨论和确认,最终我们发现该批修整器在修整砂轮时,容易出现崩口现象,这种崩口会砂轮表面形成固定高点,从而形成磨痕。
更换金刚笔,选用价格和级别更高的金刚石,问题得到解决。
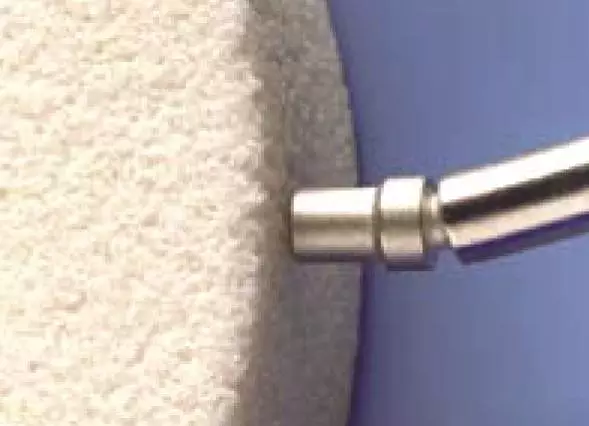
金刚石修正笔