引言
磨削是一种结合了摩擦,耕犁和剪切并利用微粒进行材料磨除的多点切削工艺。通过砂轮速度、切削深度和工作台速度等磨削参数的选择可以加工出理想的工件。除了磨削参数,修整参数对于被磨削产品的质量也有着重要影响。修整是一种加工出适宜的砂轮表面形态的工艺过程;它包括修整导程、修整深度、修整角度和修整器刃尖半径等参数;其中修整导程和修整深度尤为重要。有研究就提出“磨削即修整”的说法。在实际工业生产中,通过频繁地更换砂轮来满足被磨削产品的质量要求不太实际;此外,频繁更换砂轮也会浪费大量时间从而增加整体生产成本。因此,为了得到一个较好的表面磨削和较高的材料磨除率,对特定磨料粒度的砂轮进行修整参数优化就十分的必要。尽管有研究提出了磨粒粒度对表面光洁度和磨削力的影响,磨粒越大,表面粗糙度就越大,磨削力也就越大。但在实际生产实践中,按照被磨削产品的要求用特定粒度的砂轮进行加工几乎不太可能。本研究在众多实验研究的基础上对修整导程和修整深度参数进行了讨论研究。
本研究采用超合金英高镍718进行实验。英高镍718热强度高、抗腐蚀、抗蠕变性能好。表1是英高镍718的机械性能参数。
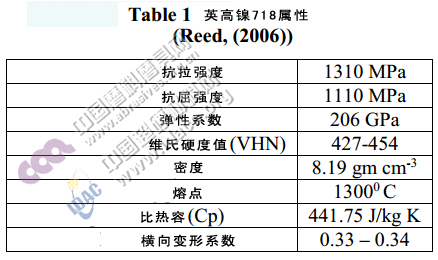
英高镍718是难加工/磨削材料,在对其进行磨削处理时需要较大的磨削力和苛刻加工硬化。高磨削力会在磨削区引起高温,而英高镍718的热传导性能比较弱,从而导致过度的热积聚并最终影响砂轮寿命。这种热积聚通过表面灼烧和拉伸残余应力的方式影响工件表面整体性能。此外,英高镍718的焊接性高,这就容易是磨粒和碎屑片粘附在一起从而导致频繁的砂轮堵塞。有时候碎屑片还会沉淀在工件表面影响表面光洁。因此,为了将砂轮堵塞降低到最小化,就需要确定适当的修整参数和磨削参数。本研究则通过实验得到最佳修整参数以实现较好的表面光整加工和较低的磨削力。
实验
磨削实验在Chevalier SMART-H1224两轴CNC平面磨床上进行。英高镍718试样为100mm×70mm×10mm;砂轮速度18m/s,工作台速度9m/min,磨削深度15μm,采用全因子分析方法选择各种修整导程和修整深度。实验采用两个因子(修整导程和修整深度)和五个水平级。利用全因子分析法实验共做了25组,修整导程值分别为50,150,250,350和450mm/min,修整深度为10,20,30,40,50μm。按照实验具体设计对修整条件进行适时调整。实验用单粒金刚石修整器进行修整,用切削冷却液进行降温处理。修整完毕再对试样进行无火花磨削。随后进行15μm深度的磨削,用压电式测力计进行磨削力测定。所有磨削实验都为顺磨。采用白刚玉砂轮A60K5V。用泰勒霍布森轮廓仪在三个不同的位置测定表面粗糙度。所有Ra测定都采用横向长度6mm,试样长度0.8mm。
结果和讨论
磨削力
图1和图2为法向磨削力和切向磨削力随修整深度的变化。图3和图4为法向磨削力(Fn)和切向磨削力(Ft)随修整导程的变化。从图表中可以看出,修整导程对磨削力的影响要远大于修整深度对其影响。
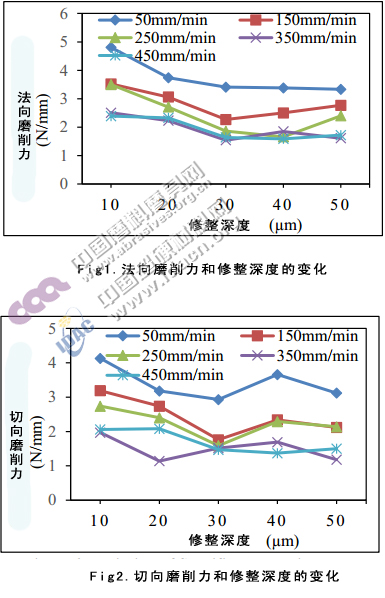
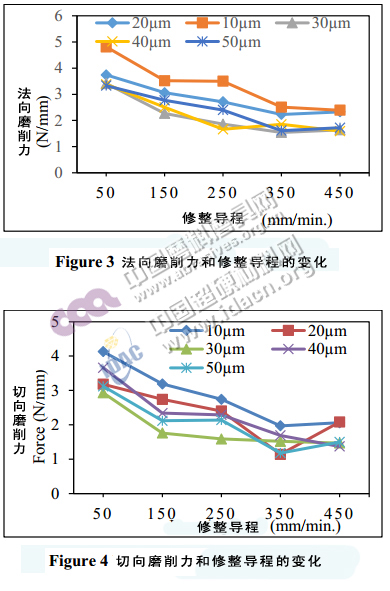
表面粗糙度
图5为表面粗糙度随修整导程的变化。细凿修整下的工件表面更光滑,而粗糙修整下的粗糙度就很大。
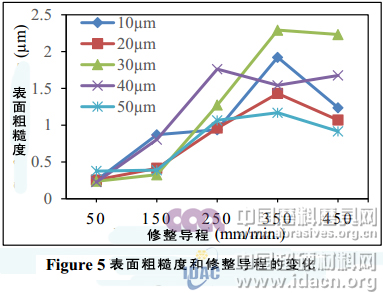
磨削力和表面粗糙度建模
利用反应曲面分类研究法(RSM)对求得的法向磨削里(Fn)、切向磨削力(Ft)和表面粗糙度值进行分析;RSM结合数学和统计学技术用于建模和分析问题, 是一种反应曲面作为输入变量的函数的序贯实验程序。
由两个因子和五个水平级求得的模型方程如下:
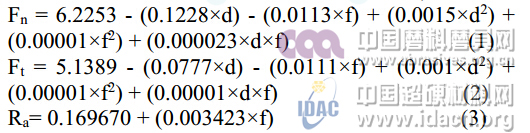
其中,Fn-法向磨削力N/mm;Ft-切向磨削力N/mm;d-修整深度μm;f-修整导程 mm/min
以上三个方程的R2值分别为92.3%、80.1%、59.2%,可以用来预测修整深度和修整导程的反应。表2为预测值和测量值之间的对比总结。实验随机挑选修整导程(f)和修整深度(d)。
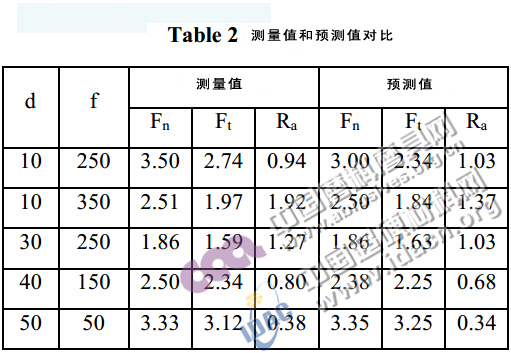
磨削力优化
未得到最优化修整参数如最小表面粗糙度或者最小磨削力,实验采用遗传算法(GA)的优化技术。在遗传算法中,统计建模求得的方程式为适应度函数,如式4、式5所示:
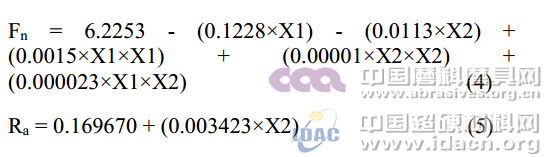
其中,Fn-法向磨削力N/mm;Ft-切向磨削力N/mm;Ra-表面粗糙度mm;X1-修整深度mm;X2-修整导程mm/min
限制条件为:10≤X1≤50 50≤X2≤450
单极优化的修整参数最佳水平为:
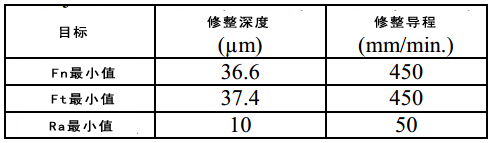
实验在规定的修整条件下利用Fn和Ra求得多目标最优化。图6为非支配点形成的Pareto front,对于Fn (2 - 2.5 N/mm) 和 Ra (0.6 - 0.8 µm)的优化范围,修整深度和修整导程范围分别落入35.5 - 37 µm 和 130 - 205 mm/min。分析Pareto front可以发现Pareto front有着典型的渐近分布和明显的分区:
•从最左边到最佳分区1,法向磨削力明显下降,对应的表面粗糙度则上升。
•从优化点到最右边,(分区3),法向磨削力上升,对应的表面粗糙度则下降。
•最佳分区2:该分区表面粗糙度和法向磨削力的值都比较稳定。
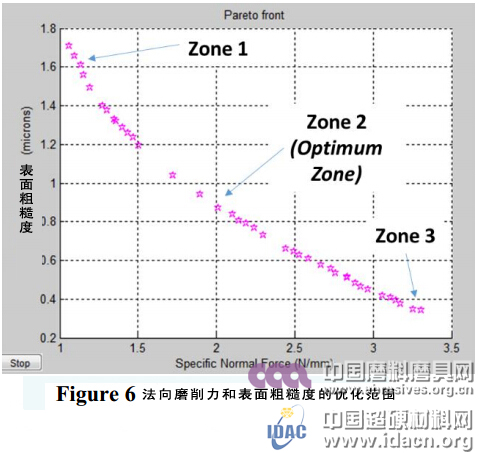
根据输出参数的要求,以上三个最佳分区都可以选择使用。例如:分区3可以用于表面精整;分区1可用于低磨削力和低温;分区2可用于中间值的表面粗糙度和磨削力。
结论
本论文研究了刚玉砂轮(磨料粒度60)的修整深度和修整导程。得出以下结论:
1、磨削力(法向磨削力和切向磨削力)受修整深度影响比较显著。对于最小磨削力,修整深度有一个最佳范围30-40μm。
2、磨削力随修整导程的增加而降低。本实验最大修整导程为450mm/min时磨削力达到最小。
3、表面粗糙度只受修整导程影响修整导程越小,表面粗糙度就越低。本实验修整导程最小为50mm/min时表面粗糙度最低。
(翻译:中国磨料磨具网)