摘要 为了研究磨削工艺参数对SiC材料磨削质量的影响规律,利用DMG铣磨加工中心做了SiC陶瓷平面磨削工艺实验,分析研究了包括主轴转速、磨削深度、进给速度在内的磨削工艺参数对工件表面粗糙度的影响。结果表明:工件表面粗糙度随着主轴转速的增加而减小,随着磨削深度和进给速度的增加而增加。在粗糙度工艺试验的基础上,以表面粗糙度最小为目标优选一组磨削工艺参数,进行了小口径SiC陶瓷非球面磨削实验,获得了较低的表面粗糙度值(0.5150μm)和较小的面形精度误差(4.668μm)。
关键词 SiC;磨削;表面粗糙度;面形误差
在现代高科技领域的光学电子技术中,光学元件是必不可少的,特别是非球面光学元件。与球面光学零件相比,非球面光学零件能够获得更好的成像质量,在光学系统中能够很好的矫正多种相差,改善成像质量,提高系统鉴别能力。它能以一个或几个非球面器件代替多个玩耍零件,从而简化仪器结构,降低成本并有效的减轻仪器重量,从而简化化妆品结构,降低成本并有效的减轻仪器重量,大大提高光电仪器的使用性能[1,2]。中小型非球面零件常用的制造方法为模压成型法,因此要实现非球面的成型,首先要制造出高精度非球面超精密模具。非球面零件模压成型模具的加工精度成为精密超精密加工领域中的一个关键性技术难题。
碳化硅材料具有较高的弹性模量,适中的密度,较小的热膨胀系数,较高的导热系数和耐热冲击性。具有高的比刚度及高的尺寸稳定性等一系列优秀的物理性质[3,4]。因此,SiC材料如何获得更好的加工质量,如何实现SiC陶瓷等硬脆材料微细模具的高精度、高效率的加工和制造,成为国内外学者们研究的方向。通过磨削工艺实验分析研究了磨削工艺参数(主轴转速、磨削深度、进给速度)对SiC陶瓷工件表面粗糙度的影响的变化规律,并以表面粗糙度最小为目标优选磨削工艺参数进行小口径SiC陶瓷非球面磨削实验,对加工表面粗糙度和耍弄误差进行了检测,得到了较好的非球面面形。
1 实验条件
1.1实验机床
本实验采用德国DMG公司型号为Ultrasonic70-5的五轴数控铣磨加工中心。
1.2 检测设备
使用泰勒霍普森公司的Form Talysurf PGI 1240型表面粗糙度轮廓仪进行工件表面粗糙度和非球面面形精度的检测。
1.3 砂轮及工件
本实验所用砂轮为电铸金刚石砂轮,工件材料为SiC陶瓷,如图1所示,砂轮参数如表1所示,其中1号砂轮用于粗加工磨削实验,2号砂轮用于精加工磨削实验。
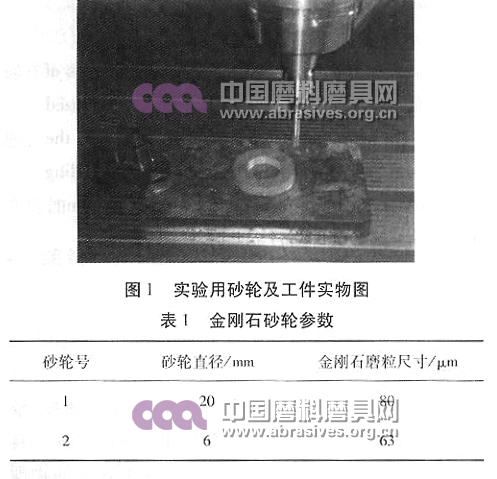
2 实验及结果分析
2.1 SiC陶瓷平面磨削工艺实验
首先,在DMG数控铣磨中心上开展了SiC陶瓷平面磨削工艺实验,研究端面铣削时SiC陶瓷表面粗糙度随磨削工艺参数的变化规律。实验所用的工艺参数如表2所示,其中粗体的参数为该参数在其他参数变化时的基础值。
表2 磨削工艺参数表
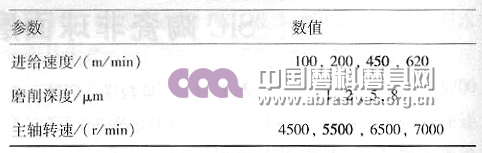
工件经平面磨削后利用轮廓仪测得的表面粗糙度检测结果(Ra 值)如表3所示:
表3 平面磨削表面粗糙度检测结果
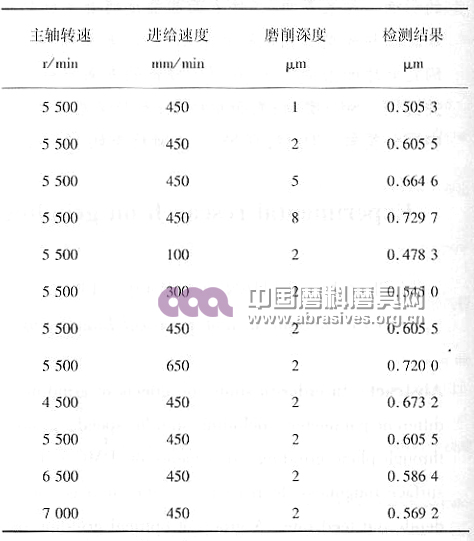
2.1.1 主轴转速对表面粗糙度的影响
主轴转速即砂轮转速对表面粗糙度有一定的影响,由图2可以看出,随着主轴转速的增大表面粗糙度值Ra减小。这是因为随着机床主轴转速的增加,磨粒磨削线速度增加,单位时间内通过磨削区的磨粒数增加,单个磨粒的磨削负荷减小,磨削力减小,从而工件表面粗糙度降低。
图2 表面粗糙度随主轴转速变化曲线
2.1.2 进给速度对表面粗糙度的影响
如图3所示,随着进给速度的增加,表面粗糙度值Ra逐渐增大,这是因为进给速度增加时磨粒磨削弧线增长,工件表面单位面积上的磨粒数目减小,单个磨粒磨削负荷增加,磨削力增加,从而使磨削表面粗糙度变大。
2.1.3 磨削深度对表面粗糙度的影响
图4所示为表面粗糙度随磨削深度变化曲线。由曲线可知,随着磨削深度的增大,加工表面的粗糙度逐渐增大。这是由于随着磨削深度增加,砂轮去除的材料体积增大,摩擦面积增大,磨削热增加,垂直于工件表面的轴向磨削力增大,金刚石磨粒的磨削的负荷增加,从而导致工件表面粗糙度增加。
2.2 SiC非球面磨削实验
根据SiC陶瓷平面磨削工艺实验结果,以SiC陶瓷磨削表面粗糙度最小为目标选择一组磨削参数进行非球面磨削实验,如表4所示。
2.2.1 非球面的选择
非球面可以分为回转对称非球面、非回转对称非球面、无对称中心非球面和阵列表面四类。其中回转对称非球面通常是一条二次曲线或高次曲线绕曲线自己的对称轴旋转所形成的回转表面。
本次实验选用二次回转对称椭圆非球面进行加工,其方程如下:

在进行非球面磨削工艺实验之前首先通过Unigraphics软件的曲面造型功能,利用参数化建模法对工件进行建模并生成数控加工程序,图5所示为软件生成的工件毛坯及非球面模型。
模型建立好之后,需要借助UG/CAM模块中的数控功能设计并生成磨削轨迹,最后根据工件模型及工艺参数自动进行加工编程。
在利用UG进行数控编程时,涉及到CAM加工环境设置、程序父节点创建、刀具选择、几何体的选择、加工方法低节点的创建、刀轨检验等方面的内容,利用UG的数控模块生成数控加工程序的流程图如图6所示。
根据图6所示流程图,创建操作方式为型腔铣操作,如图7a所示,并设置四种加工生成单元组。设定加工几何体,即选择需要加工的工件表面,如图7b所示。创建操作后,可在工件表面上生成刀具的运动轨迹,如图7c所示,图中工件表面的螺旋线为在工件上生成的轨迹。UG/CAM模块中还可以对生成的刀具路径进行验证,确认刀具位置计算的正确性,检验磨削过程是否发生过切,所选刀具尺寸、走刀路线、进退刀方式是否合理,选用的刀具与约束面是否发生干涉与碰撞。如发生碰撞重播过程停止,调整刀具的尺寸和进给参数,直到加工的过程顺利进行。
2.2.3 非球面磨削结果
在DMG数控铣磨中心上以表4所示工艺参数对SiC陶瓷工件进行非球面磨削加工,图8a、图8b分别为磨削后的SiC陶瓷非球面器件实物以及PGI1240轮廓仪实际测得的非球面面形误差,从图9中可以看出表面粗糙度值Ra为0.5150μm,非球面面形最大峰-谷误差为4.668μm。
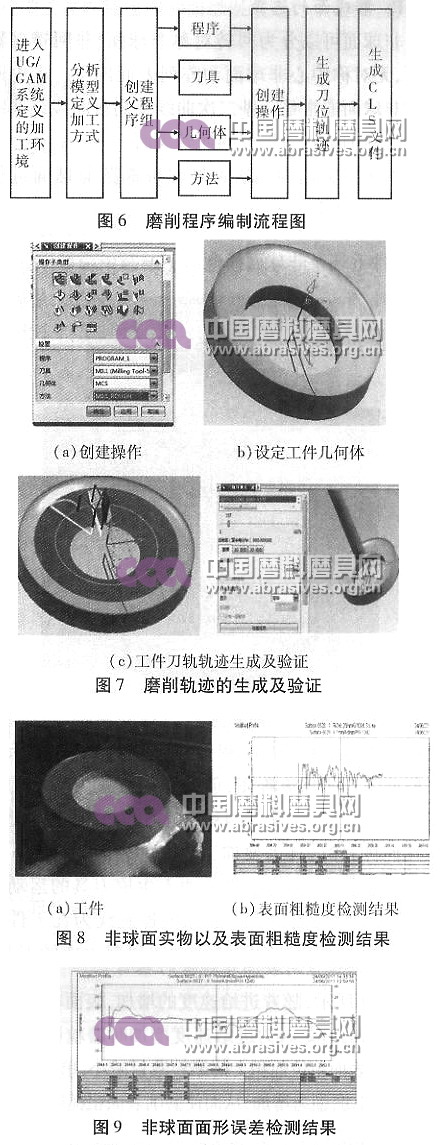
通过检测结果可以看出利用平面磨削工艺实验获得的优化磨削工艺参数进行SiC陶瓷小口径非球面磨削加工可以获得较低的表面粗糙度和较好的面形精度。
3 结论
通过SiC磨削工艺实验得出在平面磨削时工件表面粗糙度随主轴转速的增加而减小,随进给速度手磨削尝试的增加而增加;利用优选的磨削工艺参数进行SiC陶瓷非球面磨削工艺实验得到了对称椭球面的磨削表面,其中表面粗糙度Ra为0.515 0μm ,面形最大峰-谷误差为4.668μm的小口径非球面。
参考文献:
[1]潘军骅.关于非球面制造技术的看法[J].光学技术,1998(3):23-25.
[2]张坤领,林彬,王晓峰.非球面加工现状[J].组合机床与自动化加工技术,2007(5):1-5.
[3]张学军,李志来,张忠玉.基于SiC材料的空间相机非球面反射镜结构设计[J].红外与激光工程,2007,36(5):577-582.
[4] 韩杰才,姚旺,张宇民.SiC光学反射镜发展现状[J].宇航材料工艺,2005(4):1-6.
作者简介
李春慧,女,1990年出生,哈尔滨工业大学硕士研究生。研究方向:精密超精密加工。