摘要 对电镀金刚石线锯锯切微晶玻璃的工艺参数进行了试验优化研究。设计了3因素4水平的正交试验,分析了工件进给速度、锯丝线速度和气缸压力对切片表面粗糙度和锯切效率的影响,获得了基于降低表面粗糙度和提高锯切效率的锯切工艺参数。在本试验范围内,优化的工艺参数为:工件进给速度0.75mm/min、锯切线速度1.7m/s,气缸压强0.26MPa。
自从微晶玻璃出现以后,在短短的二三十年时间里,就广泛应用于电子、化工、生物医学、机械工程、军事和建筑等领域。微晶玻璃的加工越来越受到重视,由于微晶玻璃硬度高、韧性小、导热性差,加工点附近的温度容易上升,刀具的磨损较大,这决定了切割微晶玻璃的刀具不同于金属加工,不能采用硬质合金或高速钢或其他金属加工用的刀具,微晶玻璃一般采用金刚石刀具进行机械加工,这样就可以避免玻璃开裂或崩角等现象,还可以提高加工效率。
固结磨料金刚石线锯[1-2]是指通过采用某种技术或工艺方法将高硬度、高耐磨性的金刚石磨粒牢固地固结在钢丝基体表面上而制成的一种切割工具[3],非常适合加工微晶玻璃。固结磨料金刚石线锯具有切缝窄、锯切效率高、切片质量好、对环境污染小、能加工大直径工件和超硬材料等优点[4],在硬脆材料的加工方面得到了较为广泛的应用[5]。综上所述,固结磨料金刚石线锯是目前比较适合微晶玻璃等脆硬材料的切割工具。我们采用电镀金刚石线锯切割微晶玻璃,研究锯丝线速度、材料进给速度、锯丝张力与表面粗糙度和锯切效率的关系,分析影响切割表面质量的因素,为提高表面质量和锯切效率确定最优化的工艺参数。
1 试验原理与设备
采用XD-170型金刚石线旋转点切割机,实物如图1所示。锯丝运动方式为往复式,X,Y轴移动平台由双直线导轨支撑,精密丝杠/步进电机驱动,单片机控制,进给速度可无级调节,在0.025~18mm/min之间可精确控制切割厚度。X轴移动平台上装有十安夹具,可实现对棒料的夹持。本次试验使用的是横截面为正方形的棒料,切割阻力不随切割深度变化而变化,使切割面面形一致,从而实现被切材料的平整度、平行度能够达到所需的技术指标。
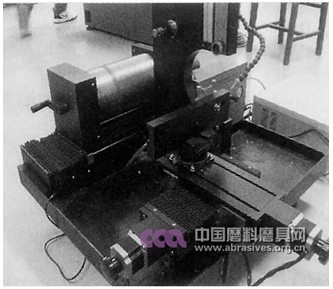
使用电镀金刚石锯丝切割微晶玻璃,锯丝直径为0.5mm,电镀金刚石颗粒的平均直径为30~40μm,工件进给速度范围为0.25~0.75mm/min,锯丝线速度为1.5~1.8m/s,气缸压强为0.2~0.26MPa。切割材料为锂铝硅系微晶玻璃,该系列玻璃具有良好的耐热性和零膨胀的特性,硬度高,但是韧性小。
实验采用德国MAHR公司生产的S3P表面粗糙度测量仪,如图2所示。能测量下列三个参数任意一个:Ra,Rmax,Rz,且可选择相互替换。可以在水平,垂直或倒置位置上进行测量,其测量范围为Ra0.02~25μm。
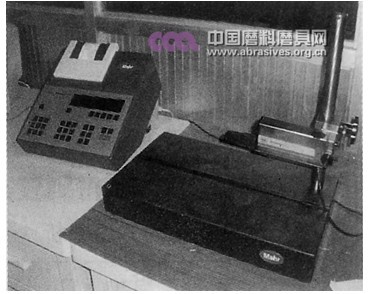
2 正交试验设计及结果
影响切片质量和锯丝寿命的锯切工艺参数有锯丝线速度、锯丝张紧力和工件进给速度等因素。为了提高锯切效率和切片质量,有必要对锯切工艺参数优化,为此,设计了一组正交试验。试验时,改变张紧支持轮的气缸压力,从而改变锯丝上的张紧力。通过控制箱上的调速装置来控制电机转速,可得到不同的锯切速度(即锯丝线速度)。由X轴移动平台的调速器来控制工件的进给速度。
影响因素:锯切速度、锯丝张紧力和工件进给速度,每个因素取四个水平,因素水平表见表1。粗糙度测量方法采用垂直切削纹路,沿进给方向依次测量三次取平均值的方法,确定微晶玻璃切片最终的粗糙度值。锯切工艺参数优化正交试验计划及试验结果见表2。
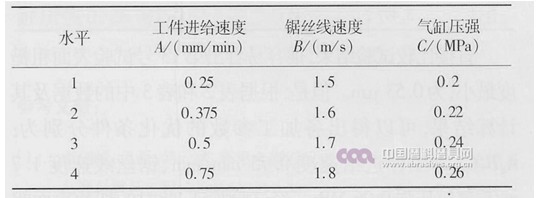

3 试验结果分析
3.1 表面粗糙度正交试验分析
对表面粗糙度的方差分析结果见表3。可见,工件进给速度对切片表面粗糙度值的影响最大。各加工参数对切片表面粗糙度的影响主次顺序依次为:工件进给速度,锯丝线速度,气缸压强。
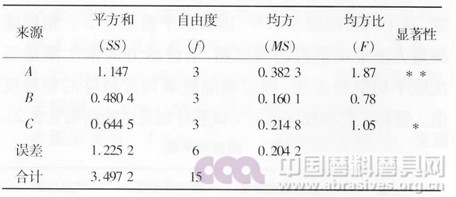
直接比较试验结果,很容易看出第13号试验表面粗糙度最小,为0.53μm。但是,根据表2和表3中的数据及其计算结果,可以得出各加工参数的优化条件分别为:A4B3C4即工件进给速度0.75mm/min、锯丝线速度1.7m/s,气缸压强0.26Mpa。经试验验证,此时的切片表面粗糙度为0.51μm,为最佳结果。切片表面形貌如图3所示。
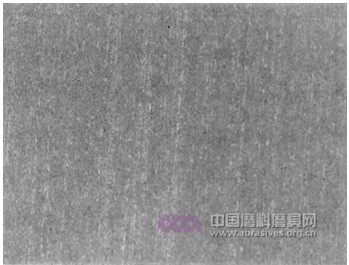
3.2 不同加工参数对表面粗糙度的影响
图4为不同加工参数下的表面粗糙度均值图。如图4a所示,在其他参数相同的条件下,随工件进给速度增大,粗糙度有小幅上升后急剧下降。主要原因是:工件进给速度增加,导致锯丝振动加剧,表面粗糙度值有所增加。当进给速度继续增加时,由于锯丝与工件之间的作用力增大,从而增大了磨料与加工表面的挤压、划擦等,锯丝变形也随之加大,导致表面粗糙度值降低[6]。
如图4b所示,随锯切丝速度提高,表面粗糙度值短暂下降之后基本保持平稳。因为线速度增加使得单个磨粒的未变形切屑厚度减小,从而表面粗糙度值减小。当锯丝线速度进一步增加时,并不能明显减小表面粗糙度值,其原因主要是,线速度增大,使得锯丝与工件之间的冲击力增大,系统振动加剧,从而破坏了锯丝相对工件的正确位置[6]。
如图4c所示,气缸压强值的大小主要反映了锯丝的张紧力的大小。张紧力越大,锯丝的振动频率随之增大,导致切片表面的纹路增加,表面粗糙度值上升。但是当张紧力达到一度阈值,振动会减小,切片粗糙度会得到改善。
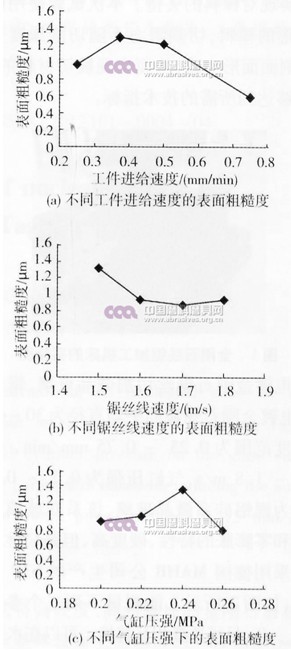
3.3 锯切效率的试验分析
由表4锯切效率的方差分析可以看出:工件进给速度对锯切效率的影响最大。其他加工参数对锯切效率的影响很小,可忽略不计。所以只要保证进给速度在工艺允许的范围内最大,就可以得到较高的锯切效率。从提高表面粗糙度和锯切效率的角度考虑,提高工件进给速度是最有效的方法。可以直接选取上述优化条件A4B3C4。
图5为不同工艺参数下锯切效率的均值图。如图5所示,随工件进给速度增加,锯切效率增加。锯丝线速度和气缸压强对锯切效率几乎没有影响,与试验分析结果一致。原因在于:平均单颗磨粒的去除量是不变的,当工件进给速度增加时,总的去除量是增加的。而锯丝线速度和气缸压强增加时并不能增加总的去除量,所以锯切效率主要受工件进给速度影响。
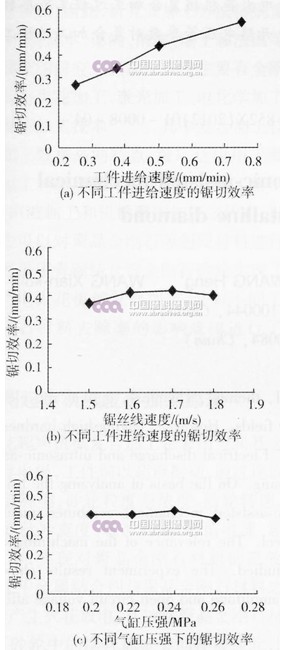
4 结论
在电镀金刚石线锯切割机床上,对微晶玻璃进行了锯切试验,用正交试验方法对锯切工艺参数进行了优化。结论如下:
(1) 工作进给速度对表面粗糙度和锯切效率影响最大,提高工件进给速度有助于降低表面粗糙度值,提高锯切效率。
(2) 锯丝线速度和气缸压强对于锯切效率几乎没有影响。
(3) 锯切微晶玻璃时,为保证较高的锯切效率和最佳表面粗糙度,在本试验范围内,最佳工艺参数为:工件进给速度0.75mm/min、锯丝线速度1.7m/s,气缸压强0.26Mpa.
参考文献:
[1] 孟剑峰,孟磊,韩云鹏。环形金刚石线锯加工参数优化[J]。金刚石与磨料磨具工程,2008(5):35-38.
[2] 赵礼刚.金刚石线锯切割半导体陶瓷的机理与工艺研究[D].南京:南京航空航天大学,2010.
[3] 高伟,刘迎.环形电镀金刚石线锯锯切工艺参数优化[J].金刚石与磨料磨具工程,2005(6):54-55.
[4] 高伟,窦百香,刘伟.固结磨料金刚石线锯制造方法和切割形式的研究进展[J].金刚石与磨料磨具工程,2008(5):30-34.
[5]ZHAO L G,ZUO D W,SUN Y L,et al.The analysis on the Stability of Diamind Wire Saw Cutting Process of the Silicon[J].Key Engineeting Material,2009,407-408:684-689.
[6] 沈兆侠,陈荣发,孙玉利,等.金刚石线锯切割对砷化镓切片表面质量的影响[J].扬州大学学报,2010,13(2):33-36.
作者简介
杨杨,男,1986年生,南京航空航天大学硕士研究生,研究方向:精密加工。