1 引言
整体硬质合金刀具在航空航天业、模具制造业、汽车制造业、机床制造业等领域得到越来越广泛的应用,尤其是在高速切削领域占有越来越重要的地位。在高速切削领域,由于对刀具安全性、可靠性、耐用度的高标准要求,整体硬质合金刀具内在和表面的质量要求也更加严格。而随着硬质合金棒材尤其是超细硬质合金材质内在质量的不断提高,整体硬质合金刀具表面的质量情况越来越受到重视。众所周知,硬质合金刀具的使用寿命除了与其耐磨性有关外,也常常表现在崩刃、断刃、断裂等非正常失效方面,磨削后刀具的磨削裂纹等表面缺陷则是造成这种非正常失效的重要原因之一。这些表面缺陷包括经磨削加工后暴露于表面的硬质合金棒料内部粉末冶金制造缺陷(如分层、裂纹、未压好、孔洞等)以及磨削过程中由于不合理磨削在磨削表面造成的磨削裂纹缺陷,而磨削裂纹则更为常见。这些磨削裂纹,采用肉眼、放大镜、浸油吹砂、体视显微镜和工具显微镜等常规检测手段往往容易造成漏检,漏检的刀具在使用时尤其是在高速切削场合可能会造成严重的后果,因此整体硬质合金刀具产品磨削裂纹缺陷的危害很大。因此对整体硬质合金刀具磨削裂纹的产生原因进行分析和探讨,并提出有效防止磨削裂纹的工艺改进措施具有很重要的现实意义。
2 整体硬质合金刀具磨削裂纹的原因分析
整体硬质合金刀具的磨削加工特点
硬质合金材料由于硬度高,脆性大,导热系数小,给刀具的刃磨带来了很大困难,尤其是磨削余量很大的整体硬质合金刀具。硬度高就要求有较大的磨削压力,导热系数低又不允许产生过大的磨削热量,脆性大导致产生磨削裂纹的倾向大。因此,对硬质合金刀具刃磨,既要求砂轮有较好的自砺性,又要有合理的刃磨工艺,还要有良好的冷却,使之有较好的散热条件,减少磨削裂纹的产生。一般在刃磨硬质合金刀具时,温度高于600℃,刀具表面层就会产生氧化变色,造成程度不同的磨削烧伤,严重时就容易使硬质合金刀具产生裂纹。这些裂纹一般非常细小,裂纹附近的磨削表面常有蓝、紫、褐、黄等颜色相间的不同氧指数的钨氧化物的颜色,沿裂纹敲断后,裂纹断口的断裂源处也常有严重烧伤的痕迹,整个裂纹断面常因渗入磨削油而与新鲜断面界限分明。传统碳化硅砂轮磨削硬质合金由于磨削效率很低、磨削力较大、自砺性差以及磨削接触区表面局部温度高(高达1100℃左右)等造成刀具刃口质量差、表面粗糙度差和废品率高等缺点已逐渐被淘汰使用;而金刚石砂轮则由于磨削效率高、磨削力较小、自砺性好、金刚石刃口锋利、不易钝化以及磨削接触区表面局部温度较低(一般在400℃左右)等优点被广泛应用于硬质合金刀具的磨削加工中。但在整体硬质合金刀具的金刚石砂轮磨削过程中,由于磨削余量很大,加工方法、金刚石工具特性和磨削制度如果选择不当,也会造成刀具磨削接触区表面局部瞬时温度偏高,从而产生磨削裂纹。
整体硬质合金刀具磨削裂纹的产生机理分析
制造硬质合金刀具采用的金刚石磨削处理可以使刀具表面层的物理?机械特性变坏或者改善。决定表面层质量的基本参数是:微观形貌(即表面粗糙度),表面层的结构和亚结构,第Ⅰ类残余应力值及其分布。烧结后的硬质合金通常具有不低于Rz5µm的表面粗糙度, 金刚石加工可以保证Rz不低于2µm,在Rz= 1~5µm范围内显微粗糙度的深度实际上不影响硬质合金的寿命指标。在磨削加工中硬质合金晶粒内部的细微结晶结构参数也发生变化,嵌晶块发生破碎(相干分散区),其值减小一个数量级,由(10~15)×10-5mm降到(10~15)×10-6mm。晶粒显微畸变值(Δd/d,第Ⅱ类应力)发生变化,表面层性能也相应变化。但是,实际上细微结晶结构参数变化与硬质合金寿命之间并未发现直接关系。所以在循环载荷下(如铣削力)硬质合金的使用寿命既与表面层的结构和亚结构无直接关联,又首先不是决定于表面粗糙度,而是决定于表面层的残余应力状态,即第Ⅰ类残余应力值及其沿截面的分布对硬质合金的强度和寿命起着决定性因素。表面层残余压应力的形成促使断裂源迁移到距离表面更深的受载荷较小的层次,抑制了裂纹的萌生和扩展,这就使得强度和寿命增加;同时随着硬质合金表面层残余压应力层分布深度的增加,其强度和寿命逐渐提高。而表面层形成的残余拉应力则促进裂纹的萌生和扩展,是产生裂纹的必要条件,且使得强度和寿命降低。但磨削后的表面往往既有残余压应力又有拉应力,因此,理想的磨削表面层状态应是表面层残余压应力值越高越好,残余压应力层分布越深越好;近表面层残余拉应力值越低越好,残余拉应力层越薄越好,最大拉应力值距离表面越深越好。反之,表面层较浅的压应力分布和近表面层过高的拉应力值则是萌生磨削裂纹的主要原因。所以,在磨削加工过程中应尽量减小和避免残余拉应力的产生。
在多数情况下硬质合金制品烧结后在表面层产生残余拉应力(起源于热),这种拉应力值可达500~1000MPa。该应力层的深度不大于5~7µm,应力渗入深度不超过30~40µm。越接近表面,其值越高;钴含量越高,其值越高。因此烧结后的硬质合金抗弯强度值(TRS值)和疲劳寿命值很低。但磨削余量常大于0.1mm,因而随后的磨削加工在去除硬质合金表层后完全可以消除烧结合金中的残余拉应力,并形成新的应力状态。由此可见,烧结工艺引起的残余应力对在磨削过程中残余应力的形成没有影响。
在磨削加工过程中,影响刀具表面状态的有两个主要因素:施加的力和局部温度。施加的力对合金表面的作用会引起不可恢复的塑性变形、结构的变化和相变并伴随着单位体积的增大,从而导致形成残余压应力,提高抗弯强度、疲劳强度、冲击韧性、硬度、耐磨性和使用寿命等,亦即发生强化过程;局部温度对合金表面的作用会在表面层中产生不均匀的热塑性变形、结构和相的变化并伴随着单位体积的减小,从而导致形成残余拉应力、降低抗弯强度、疲劳强度、冲击韧性、硬度、耐磨性和使用寿命等,亦即发生弱化过程。因此,硬质合金刀具最终表面层状态是被强化还是被弱化,是残余压应力为主,还是残余拉应力为主,则取决于在磨削过程中对其表面的作用是以力为主还是以温度为主。当磨削过程中磨削接触区的局部瞬时温度达到一定程度(有时可达1000℃以上)占主导因素时,便会形成表面层较浅的压应力分布和近表面层过高的拉应力值,残余拉应力促进裂纹的萌生和扩展,其数值之大,甚至会超过材料的破断强度,而形成细微小裂纹。有时在磨削后不产生裂纹,但在研磨或使用过程中,当其表层被去除后,下层的残余应力失去平衡,才出现裂纹。在金刚石加工时,刀具表面磨削接触区局部瞬时温度的高低将取决于加工方法、金刚石工具特性和磨削制度。
3 整体硬质合金刀具磨削裂纹的无损检测
通过以上分析以及大量的检测试验,我们采用高灵敏度的亲水性后乳化荧光渗透探伤法对采用相同磨削工艺(未改进前)的近万件同一材质刀具的对比检测结果表明其磨削裂纹检出率最高(见表1)。对使用我们经后乳化型荧光渗透检测合格的整体硬质合金刀具的用户进行回访,也未反映发生过因刀具裂纹等表面缺陷造成的刀具崩刃、断刃、断裂等现象。这些情况表明采用高灵敏度的亲水性后乳化荧光渗透探伤法无损检测整体硬质合金刀具的磨削裂纹缺陷是有效的。刀具后乳化型荧光渗透检测工艺流程如图1所示,检出的整体硬质合金铣刀典型磨削裂纹如图2和图3所示。
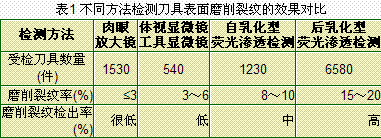

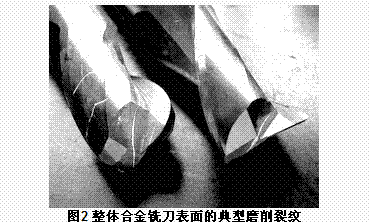
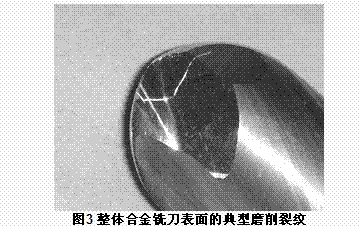
4 整体硬质合金刀具磨削工艺改进
影响磨削裂纹的磨削工艺因素
如前所述,整体硬质合金刀具表面的磨削裂纹主要是由于磨削过程中磨削接触区的局部瞬时温度过高形成磨削表面层较浅的压应力分布和近表面层过高的拉应力值超过材料的破断强度造成,因此,在磨削加工过程中应尽量减小和避免瞬时高温的产生,也就减小和避免了残余拉应力的产生。磨削过程中的瞬时高温往往会引起磨削表面层的机械性能的变化,这种瞬时高温可达1000℃以上,对刀具表面层造成磨削烧伤。磨削烧伤会破坏刀具表面层组织,使工件表面的质量恶化,严重影响刀具的强度、耐磨性和使用寿命;严重时还会产生裂纹。因此,不仅要防止产生磨削裂纹,还必须避免磨削烧伤。在金刚石加工时,刀具表面局部瞬时温度的高低将取决于加工方法、金刚石工具特性和磨削制度。
实践证明:金刚石砂轮的线速度和径向进给量越大、砂轮硬度越高、砂轮粒度越细、刀具材料导热系数越低和砂轮磨损得越厉害,都使磨削温度升高得越厉害,则越容易产生磨削裂纹及磨削烧伤。要控制和避免磨削裂纹及磨削烧伤,必须采取两方面的措施:一是减少磨削热的产生,二是加速磨削热的传出。减少磨削热的办法是:适当降低金刚石砂轮的线速度,减小径向进给量(粗磨?精磨?抛光分工序进行),选取较软的金刚石砂轮,减少工件和砂轮的接触面积,根据磨削要求合理选择砂轮的粒度,经常保持砂轮在锋利的条件下磨削以及选择适宜的磨削冷却液以减小磨粒与工件间摩擦等。加速磨削热传出的措施是除了适当提高工件速度和轴向进给量外,主要是采用有效的冷却方法;为了提高冷却效果,可采用喷雾冷却、高压冷却、内冷却以及运动粘度较低的冷却油等。另外,在精磨时,减少进给量和适当的光磨,可有效减少表层内残余应力。
综上所述,为了提高生产率和磨削效率,同时又要获得较好的磨削表面质量,我们的方法是一开始采用较低的砂轮线速度和较大的径向进给量,最后几次进给量减小而砂轮线速度提高,并进行光磨,这样可提高磨削表面质量。为了进一步提高磨削表面质量,还可采用喷雾冷却和高压冷却,选择适宜的切削液,同时根据加工对象合理选择砂轮和精细地修整砂轮。磨削参数的选择原则是:磨削参数是在保证磨削温度较低、磨削表面粗糙度较高的条件下,尽量选取较低的砂轮线速度,较大的径向进给量、轴向进给量和工件速度。由于砂轮的线速度和径向进给量对磨削表面层的质量影响最大,因此,磨削参数的选择步骤是:先选较大的工件速度,再选轴向进给量,最后才选砂轮线速度和径向进给量。
防止磨削裂纹的磨削工艺改进措施
选用合适的冷却液和冷却方式
将国产冷却油更换为运动粘度更低的进口冷却油,并改进冷却方式,使冷却油始终处于磨削接触区冷却,油温控制在2315℃以下(空调风冷控制),同时增加工具磨床油泵压力,以加强磨削中的冷却效果。
选用合适的金刚石砂轮金属粘结剂金刚石砂轮由于导热性好、磨削力大、磨削效率高,主要用于粗开槽工序(磨沟槽)的粗磨和精磨,该工序也可选用高温树脂粘结剂金刚石砂轮,但磨耗较大;树脂粘结剂金刚石砂轮润滑性好,磨削力较小、自砺性好,选用中等、中软树脂粘结剂金刚石砂轮或勤修砂轮,始终保持砂轮处于锋利状态,主要用于开齿工序(前后刀面、端齿槽、偏背去余量等工序总称)的粗磨和精磨。金刚石砂轮浓度选择75%~100%,金属粘结剂砂轮粒度选择120~140目,树脂粘结剂砂轮(RVD)粒度粗磨选择80~120目,精磨选择200~240目较为合适。若全部选用质量较好的进口砂轮,则刀具的磨削效率和表面粗糙度均高于国产砂轮。
选择合理的磨削参数
以在德国SAACKE公司的UWIE212型数控工具磨床(15kW)上磨削整体硬质合金两刃螺旋立铣刀为例,粗开槽工序(磨沟槽)金刚石砂轮线速度选择14~20m/s ,机床轴向进给速度选择50~200mm/min,机床径向进给量粗磨选择210~510mm,精磨选择0.2~0.5mm;开齿工序(前后刀面、端齿槽、偏背去余量等工序总称)金刚石砂轮线速度选择14~24m/s,机床轴向进给速度选择100~400m/min,机床径向进给量粗磨选择0.3~1.0mm,精磨选择0.05~0.1mm。磨前后刀面时还采用无进给返程光磨提高其表面粗糙度。如选用进口砂轮,允许选择比国产砂轮偏高的砂轮线速度和较大的径向进给量。
磨削工艺改进措施的效果验证
磨削工艺改进后的6800余件整体硬质合金刀具(其中有近4000件为高速铣刀)采用同一种后乳化型荧光渗透检测法进行探伤。结果表明:不仅刀具磨削表面质量大为改观,磨削裂纹率由工艺改进前的将近20%逐步降低为工艺改进后的15%、10%、6% ,直至最佳改进工艺的0.5%以下,刀具表面磨削烧伤情况(发亮、发白而不是发蓝、发紫、发褐、发黄、发乌、发暗)以及表面粗糙度情况(Rz0.2~0.8µm)也显著改善;而且磨削效率还有所提高,以直径20mm的两刃整体硬质合金高速铣刀为例,工艺改进前完成每件刀具的磨削需要30~40min,工艺改进后则只需20~30min,如果都采用质量较好的进口冷却油和进口金刚石砂轮,最佳改进工艺对应的磨削效率还可提高到每件14~20min。
5 结语
整体硬质合金刀具产生磨削裂纹的主要原因为磨削工艺和参数不恰当导致磨削接触区的局部瞬时温度过高引起近表面层过高的拉应力值超过材料的破断强度造成。
采用高灵敏度的亲水性后乳化荧光渗透探伤法可有效地检测整体硬质合金刀具的磨削裂纹等表面缺陷;推荐该方法广泛用于整体硬质合金刀具的质量保障技术领域。
通过改进和优化整体硬质合金刀具磨削工艺和磨削参数可有效防止磨削裂纹及磨削烧伤的产生。