摘要 在能源短缺和环境日益恶化的今天,风能作为一种新型的可再生清洁能源,被誉为21世纪最有发展前景的绿色能源,越来越受到世界各国的重视。全球风电行业的快速发展,对所用轴承提出了更高的要求...
在能源短缺和环境日益恶化的今天,风能作为一种新型的可再生清洁能源,被誉为21世纪最有发展前景的绿色能源,越来越受到世界各国的重视。全球风电行业的快速发展,对所用轴承提出了更高的要求,尤其是应用在兆瓦级别的风力发电机上的轴承,只有极少厂家才具有技术能力试制。图1为风力发电机结构图,表1为风力发电设备应用轴承的主要区域及要求汇总。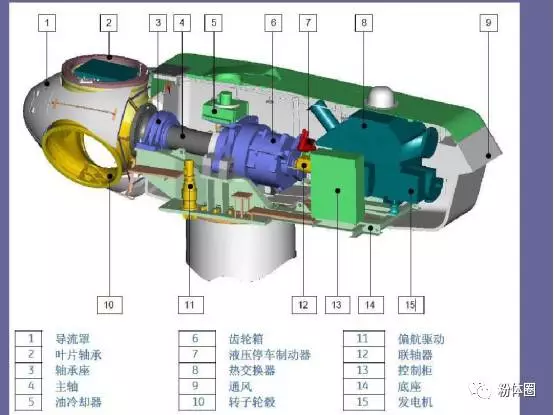
图1 风力发电机结构图
表1 风力发电设备应用轴承的主要区域及要求
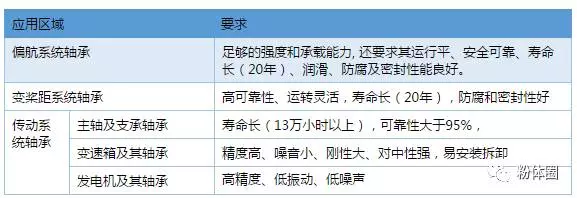
据国家能源局处消息称,2012年以来,我国新增风电装机容量连续4年居世界第一,领跑全球。截至去年底,我国风电累计新增装机容量8758万千瓦,成为煤电、水电之后的第三大电源。国内在大功率并网风力发电机的相继投入,风力发电氮化硅单单就轴承球国内外的市场就将有望突破200万粒,市场容量每年超过10亿元。
氮化硅陶瓷材料应用在风电行业轴承中的情况主要分为两类:氮化硅陶瓷轴承(图2)、氮化硅陶瓷滚动体与钢制轴承底座制成的混合陶瓷轴承(图3)。氮化硅陶瓷轴承是指内外圈、滚动体采用氮化硅陶瓷材料,保持器采用不锈钢、尼龙、氧化锆、氮化硅或特定铝合金制成的轴承,其性能比混合陶瓷轴承佳。
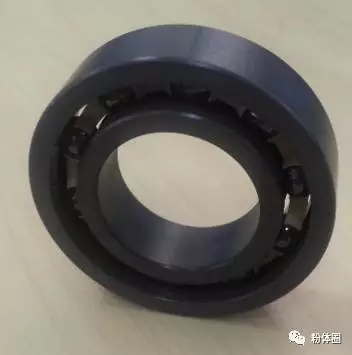
图2 氮化硅陶瓷轴承
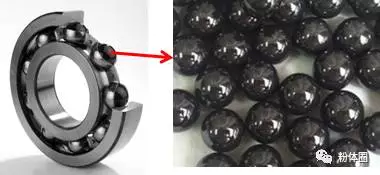
图3 氮化硅滚动体与钢制材料组成的混合陶瓷轴承及氮化硅球
1、轻质耐高速:氮化硅的密度仅为3.19g/cm3,相对于轴承钢7.85g/cm3具有的轻质优势所产生的离心力更小,使用与高速旋转设备,且不易出现“抱轴”;
2、低热膨胀系数:在100-800℃间低热膨胀系数有助于防止其卡死,能更好的应用在风力较大区域的风电设备上;
3、高强度:氮化硅的高抗压强度是大型风力发电设备中高接触应力滚动轴承所需要的。
4、高硬度:2倍于轴承钢硬度,满足风力设备在外界环境中粒子冲击及滑动摩擦损伤;
5、耐高温:轴承的疲劳寿命受到温升变化的极大影响,在1000℃下氮化硅轴承还具有良好的接触应力和使用寿命;
6、耐腐蚀:氮化硅具有极强的耐腐蚀能力,对大多数酸、碱具有优异的稳定性,应用在风电行业,可抵抗雨水等侵蚀;
7、自润滑性能好:氮化硅材料在润滑条件差的情况下具有减摩、润滑功能,提高轴承的可靠性和寿命,同时减低噪声。
表2 氮化硅与其它陶瓷材料及钢材料的基本性能对比
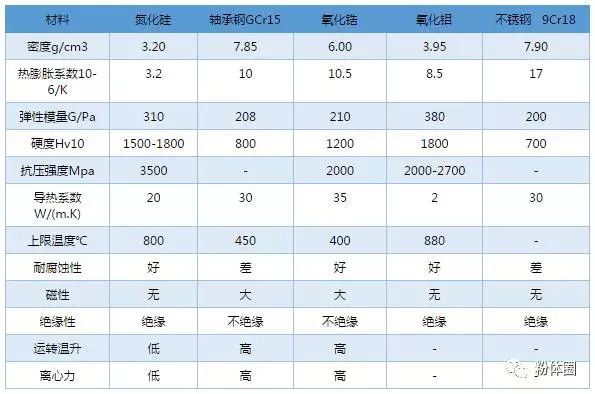
二、氮化硅轴承的制造工艺流程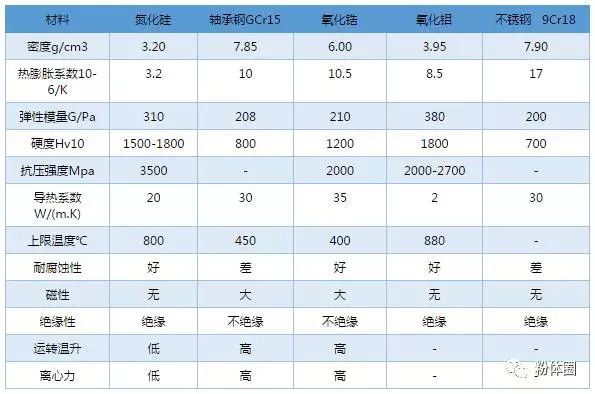
氮化硅陶瓷轴承的制造过程涉及较多过程,包括原料粉末的配置混合、坯体成型、坯体烧结、磨削精细加工、精密检测等主要流程,具体见下图4。
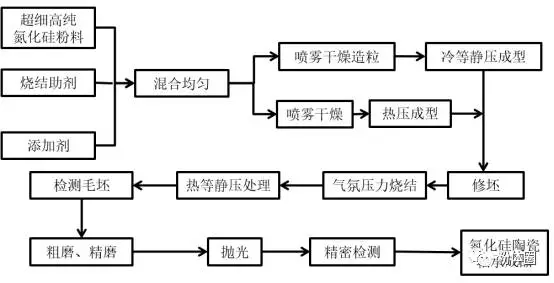
图4 氮化硅陶瓷轴承球制备工艺流程
氮化硅陶瓷轴承的化学成分包括氮化硅和烧结助剂,原始粉末中Si3N4常以金属硅氮化法、氧化硅还原法、亚胺热分解法、气相法等方法制备,以α型Si3N4为佳。制备的Si3N4粉末中含有的Fe、Al、Ca等杂质降低了氮化硅轴承的高温强度,且削弱了耐氧性能。烧结助剂有MgO、Y2O3粉末及C、SiC、ZrO2等纤维,下面为制作氮化硅轴承烧结体较常用的成分:
(1)Si3N4+MgO+AlN+ Y2O3,其中Y2O3为主要烧结助剂成分,得到的轴承机械强度与硬度高;
(2)Si3N4+SiO2+SrO+CeO2+MgO或Si3N4+SiO2+SrO+CeO2+ZrO2,烧结助剂总量控制在2%-10%;
(3)Si3N4+SiO2+第ⅢA主族氧化物,得到抗弯强度和韧性均好的烧结体。
2、成型和烧结
氮化硅陶瓷轴承的成型和烧结主要分为热压及热等静压方法、先冷压成型后在N2或惰性气氛环境中常压烧结的方法。
(1)热压烧结:这是目前制造氮化硅陶瓷轴承应用最多的方法,温度一般在1600-1800℃,保温15min-1h,在石墨模中的压力一般为20-40MPa,且常用BN作为脱模剂。优点是烧结温度低,添加烧结助剂用量少,致密度高,耐磨和抗疲劳性能优良。
(2)热等静压:压力方向不受限制、可施加压力大(50-200MPa)、烧结温度低(1750-1800℃)。但设备费及运转费用昂贵,制造的氮化硅陶瓷轴承多用于实验室研究阶段。
(3)常压烧结:先将干燥造粒的混合粉末再150-500MPa压力下成型,制成接近最终形状的预制件再进行烧结,烧结温度较高,且需要N2或惰性气体防止Si3N4高温氧化。优点是无需模具、生产效率高,但缺点是轴承质量较差。
3、精加工和无损检测
氮化硅陶瓷轴承的优异物化性能决定了其多应用在精度要求高的环境下,故需对烧结后的氮化硅陶瓷轴承的套圈、滚动体等毛坯进行精密加工。先在树脂结合剂金刚石砂轮的磨床上磨削以提高其烧结制品的尺寸精度,后在以金刚石磨粒的研磨机上精研磨和采用细粉磨粒抛光,最后在进行陶瓷轴承的无损检测。
在ASTMF 2094/F 2094M-08 标准中,将氮化硅陶瓷球的缺陷分为夹杂、疏松、各类划痕和小坑、裂纹和色差等5大类加以控制,采用光学检查、荧光穿透性检查和超声检查等检测方法控制表面质量,其中光学检查依然是目前高可靠性陶瓷球的主要检查手段。图5为陶瓷球检测示意图,图6为陶瓷缺陷显微照片。研究表明,Si3N4陶瓷的抗疲劳能力需要杜绝在主承载区域内5μm以上的显著缺陷。高级检测手段包括高精度X射线无损探伤技术、表面波声成像技术和扫描电子声发射技术。
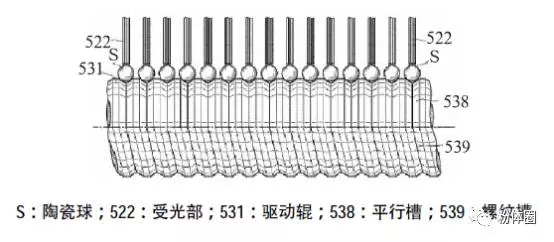
图5 Si3N4陶瓷球检测示意图
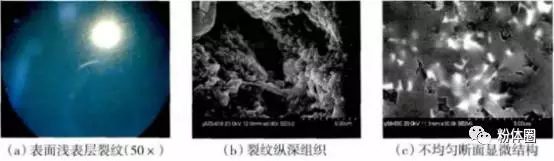
图6 Si3N4陶瓷缺陷显微图
自上个世纪70年代,国外研究学者已经在氮化硅陶瓷轴承,研究的重点放在了全氮化硅陶瓷轴承、氮化硅滚动体与其它材料的混合轴承性能及陶瓷轴承的设计理论上。目前世界上生产、研究、销售氮化硅陶瓷轴承的公司有很多,如瑞典的斯凯孚(SKF)、德国的舍弗勒(FAG)、美国CoorsTek、日本的精工(NSK)公司等,NSK公司已经有28个规格3种级别的角接触球轴承供用户选择。国内在“八五”期间将“陶瓷轴承”列为国家科技攻关计划,上海硅酸盐研究所等开始了氮化硅陶瓷轴承的研究,目前已经实现产业化的企业主要有中材高新、上海泛联、中兴实强等单位,但产品质量与国外相比还有较大差距,尤其是高端氮化硅陶瓷球90%依赖尽快,规模化生产技术还存在较多问题,如下:
1、高品质氮化硅粉体受限:我国主要采用硅粉氮化法制备氮化硅粉体,但纯度低、球形度差、烧结温度高等缺点;相比日本的宇部兴产株式会社是唯一利用化学合成法制备的粉体产品质量高,是制备高精度氮化硅轴承的首选材料,但其对华严格限制供货量,阻碍了国内氮化硅陶瓷轴承的发展;
2、氮化硅陶瓷球成型效率低:坯体球形度差、产量低,尤其是2mm以下的小球,轴承球精度仅仅为G5水平,而SKF等公司的氮化硅轴承球的精度可达G2级,配套的精密轴承噪音小、转速高、寿命长,综合性能明显优于国内;
3、检测手段落后:氮化硅具有的无磁、绝缘等性质使其在快速生产过程中快速无损检测的要求更高,国内依然采用人工显微镜检验,而国外已经实现了自动化的快速连续无损检测,差距较大。
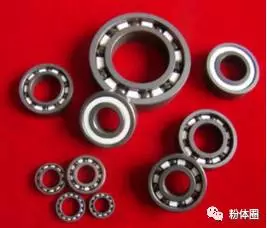
图7 我国生产的Si3N4陶瓷轴承
表3 国外公司在氮化硅陶瓷轴承方面部分专利
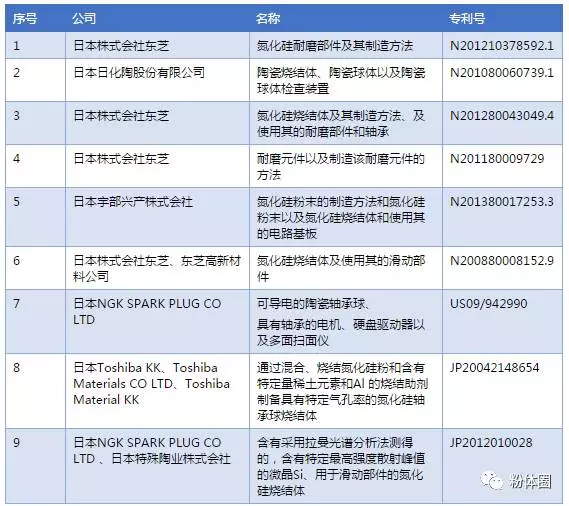
四、氮化硅陶瓷轴承发展趋势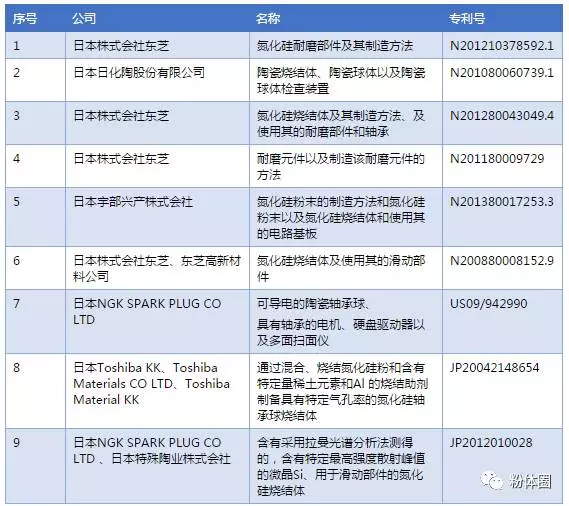
氮化硅陶瓷轴承因其具有的热稳定性能好、抗氧化能力强、耐磨性能好、能自润滑等优异性能在风电、航空航天、核电等领域得到了广泛的应用,具有巨大的潜力,未来的氮化硅陶瓷轴承的发展趋势主要包括:
(1)高韧高强材料技术:在现有氮化硅粉体中减少Fe、Al等杂质元素、提高α相含量、高球型度和粒径分布相对集中,经热等静压烧结,可得到性能更佳的氮化硅毛坯材料。
(2)低成本批量稳定生产技术:包括全寿命期研发费用、产品费用和维修费用等在内的氮化硅陶瓷轴承的高成本依然是制约其大面积应用的主要因素,实现低成本批量的稳定生产可促进氮化硅陶瓷轴承在各行各业大显神通。
(3)健康管理技术:在风电行业、航空航天等领域,对氮化硅陶瓷轴承的应用环境和条件提出了越来越苛刻的要求,氮化硅轴承性能的波动和轴承失效都会导致严重的系统问题或者失效,建立轴承的健康管理系统轴承和齿轮的健康状态监测是重要的解决方案。
(4)无损检测:在严苛条件下使用的氮化硅陶瓷轴承需要先进且有效的无损检测手段,配合现有的自动化设备,形成完整的智能化无损检测体系。
作者:弋木
参考文献
1、 利用国外专利技术解决国内氮化硅陶瓷轴承球产业化问题,李贵佳等。
2、 氮化硅陶瓷的制备与应用,孙亚光等。
3、 浅谈氮化硅陶瓷轴承制造技术,栾景燕等。
4、 陶瓷轴承球的应用和生产加工,徐学敏等。
5、 轴承用理想材料-氮化硅陶瓷,季德振等。
6、 混合型氮化硅陶瓷轴承的新进展,张宝林等。
7、 高可靠性陶瓷轴承技术研究进展,王黎钦等。
8、 国外氮化硅陶瓷轴承的发展概况,肖旭东等。
9、 特殊要求用混合陶瓷轴承与全陶瓷轴承,刘家文。