引言
聚晶金刚石(PCD)是金刚石微粒在高温高压下(1450-1750℃;5.5-8.0GPa)由金属结合剂粘合而成。由于其硬度高韧性好,PCD常用于木材加工、油气钻探和汽车工业有色金属合金的加工。在制造PCD时,将金刚石微粉放置在钨/钴衬底上,烧结过程中衬底上的钴融化并渗入金刚石层,从而使金刚石颗粒粘合在一起。
PCD虽然性能优越,但在超过700℃的高温下时会受热不稳定性影响,从而导致耐磨性降低,工具寿命缩短。对于PCD材料而言,一般会有两次高温影响,第一次是制造PCD工具时,利用高温钎焊将PCD加工成工具;第二次是钻削时摩擦生热。
早前已有一些对金属烧结助剂影响PCD热稳定性影响的研究,以及对此影响做出解释的两种假设。金属烧结助剂的热膨胀系数(α)通常要比金刚石高很多,在温度上升过程中,钴(α=14×10-6/℃)比金刚石(α=1×10-6/℃)膨胀更强烈,从而引起裂纹和微碎裂。另外,钴还会分解金刚石微粒并转化其为石墨;金刚石转化为石墨的过程中有一个3.6g•cm-3到的2.0g•cm-3的密度变化,体积膨胀就会加大对金刚石结构的力度,从而引起材料裂纹。
实验已经采用几种办法来解决PCD热不稳定性的问题。一种是通过酸滤取部分或全部去除钴,另一种方法是没有钴烧结助剂的条件下烧结。超硬纳米聚晶金刚石(NPD)材料是在高温高压(2300℃;15GPa)下直接将石墨/含碳材料转化为金刚石;第三种方法是用陶瓷相替代金属结合剂。
本实验旨在研究PCD材料在温度上升过程中的热降解机理,并做了热稳定性测试。实验第一部分是PCD工具热机械研磨测试,第二部分是在电子显微镜和X射线衍射帮助下对PCD化学成分变化做了研究。
实验材料和方法
长度为16mm直径为16mm的柱形PCD钻头刀片;每个刀片都有一层2mm厚的硬质合金基体PCD覆层。将粒度为10μm的金刚石微粒放置在钨-钴衬底上,5.5GPa/1450℃的条件下处理10分钟,钴含量为12wt.%。
热机械研磨实验
研磨实验在抗压强度为200MPa的花岗岩上进行,不使用冷却液。将加工参数调整为PCD工具能够在工作过程中产生高温的值。PCD刀具在加工平面上的纵向前角为10°,转速1140rpm,切削深度2.5mm,进给速度0.04mm/rev。PCD切割工具相对花岗岩的切割几何形状如图1所示。
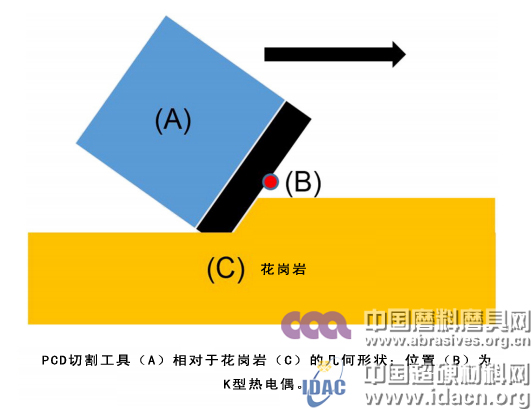
K型热电偶接触金刚石表面(位置B)测得温度并将其作为切割时间的一个函数。相同的工具用于每一个测试,测试在400℃,500℃时停止,在600℃时失败。每一个工具都用电火花加工取得横截面然后进行抛光处理以做微结构分析。用Ga+离子-聚焦粒子束(FIB)扫描电镜进行薄片处理以供透射电镜对磨痕降解区进行研究。基于电子能量损失能谱的扫描投射电子显微镜用来确定加工过程中形成的相。
氩气热浸
实验第二部分从PCD刀片上获取几个3mm直径的圆片,将其切削成100μm厚度。在热处理之前先用X衍射进行试样监测以建立试样化学成分。检测结果发现热处理之前的试样有着类似的组份(相和晶胞参数)。然后将试样放在管状石英炉中,氩气环境下进行加热,氩气流量设置为2 l/s。随后将试样放入冷却区15分钟以去除残余的氧,然后再放去加热区。700℃、750℃、800℃和850℃下分别放置2小时以研究温度对材料热降解的影响。此外,再选试样在800℃下分别放置0.5小时、2小时、4小时和6小时以研究时间对材料热降解的影响。热处理之后用X射线衍射(λ=1.789Å)进行钴晶胞参数和相的测定。
用PIPS™ 型离子减薄仪对试样进行机械抛光至电子透明程度,然后进行TEM研究。用电子衍射和能量色散谱对试样的碳化物析出物进行表征,用STEM-EELS光谱成像对石墨碳相进行研究。
实验结果
图2为PCD材料微结构的反向散射SEM图。根据材料抛光面的反向散射SEM分析,该材料的结合剂总含量为9±1vol.%。
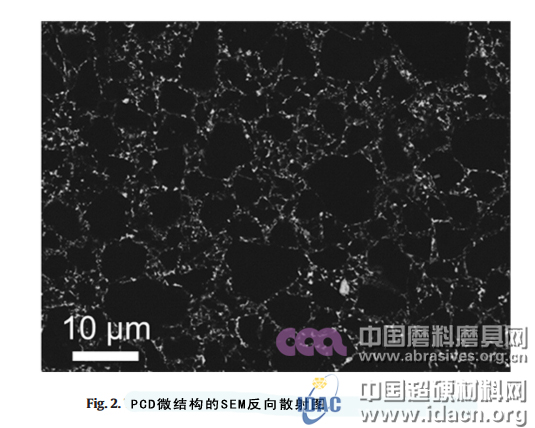
热机械研磨实验
实验第一部分对PCD工具进行了研磨试验,将热电偶放在金刚石表面中心测得花岗岩和PCD工具界面的温度。然后在显微镜下对抛光横截面进行观察,如图3a-c。工具温度在400℃以下时无明显裂纹(图3a);500℃时切割界面出现模糊的裂纹(图3b);温度继续上升直至实验失败时出现大量裂纹并导致密集的结构降解(图3c)。这些裂纹也意味着切削效率和工具寿命的降低。
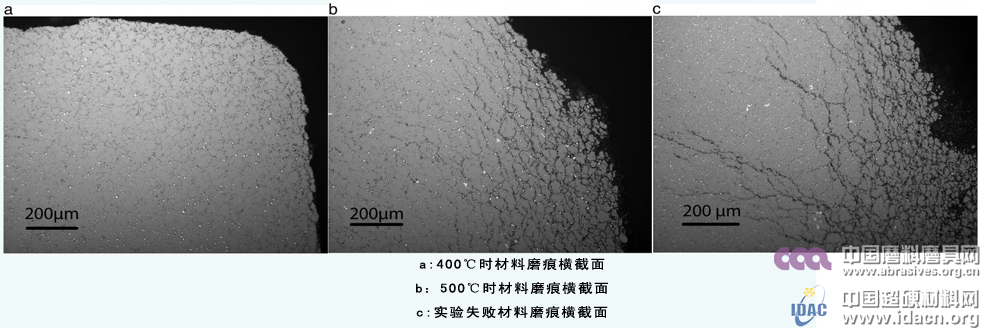
为研究裂纹出现的机理,从500℃时的样式上获取一段FIB切片如图4所示。由SEM二次电子像可以看出裂纹成间粒状,但也观察到了穿晶扩展的裂纹。图5为STEM高角环形暗场像。进行STEM–EELS光谱成像并把各种化学相映射在感兴趣区,刀片显示了一个各种相的色彩图:钴(红色),石墨(青绿色),金刚石(绿色)。很明显可以看出金刚石转化为石墨的过程发生在这一区域。这表明接触面产生的温度足以使钴能够催化地和金刚石发生反应从而形成石墨。这也证明了之前的一个假设,金刚石的石墨化导致了裂纹,而并非完全是热膨胀的缘故。
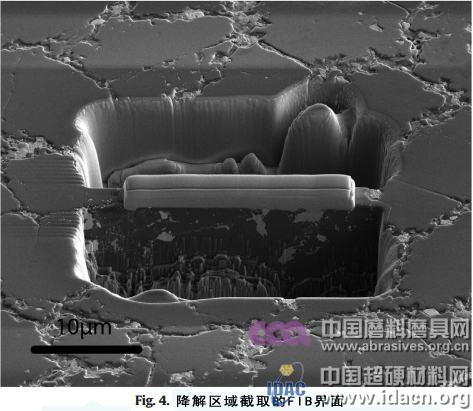
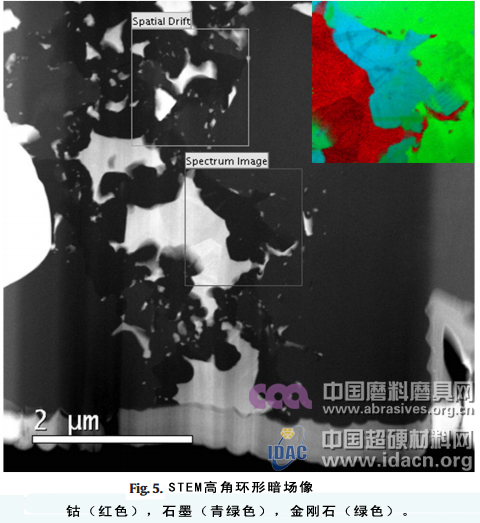
氩气热浸
热处理之前对试样进行X射线衍射,观察发现钴的晶胞参数从理论值3.54 Å增加爱到纯fcc钴3.59 Å如图6所示。这主要是由于固溶体钨的原因。在烧结过程中,熔融钴分解了衬底WC/Co上的一部分钨和碳。高温烧结过程中额外的钨也从衬底分散到了金刚石层上从而引起固溶体钴中出现了钨和碳。钨原子置换式融入钴(2-15wt.%,125℃),碳原子间隙式融入钴(0-0.2wt.%,上升温度)。固溶体元素预计会提高钴晶胞参数。本研究中钴晶胞参数的增长主要是由于固溶体钨的原因。这一预计主要是由于钨散射因子导致钴相峰高度的增加而引起的。如果主要影响是固溶体碳,那么钴峰高度就不会增加,因为碳的散射因子要比钨低很多。
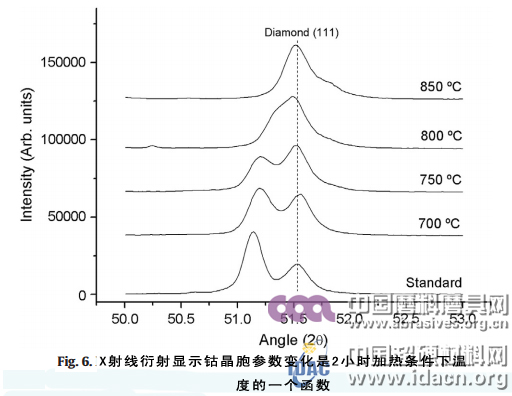
PCD试样分别在700℃、750℃、800℃和850℃下加热2小时,每个试样得出的室温X射线衍射类型如图6所示。随着试样被加热到设定的温度,钴晶胞参数逐渐降低。850℃加热2小时后钴晶胞参数为3.54Å,相当于纯钴的值。此外,在温度处理过程中η相(Co,W)6C沉淀。该相的峰高度作为温度的一个函数,如图7所示。
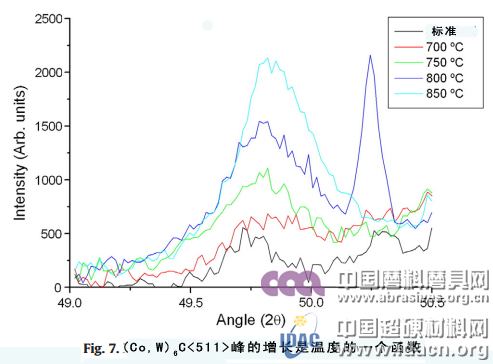
再取试样在800℃下分别加热0.5小时、2小时、4小时和6小时。得到的室温X射线衍射类型如图8所示。钴晶胞参数随着时间逐渐降低,800℃下加热6小时后晶胞参数为3.54 Å,这说明钴晶胞参数变化至纯钴值。在温度处理过程中再一次观察到η相(Co,W)6C沉淀。该相的峰高度作为时间的一个函数,如图9所示。
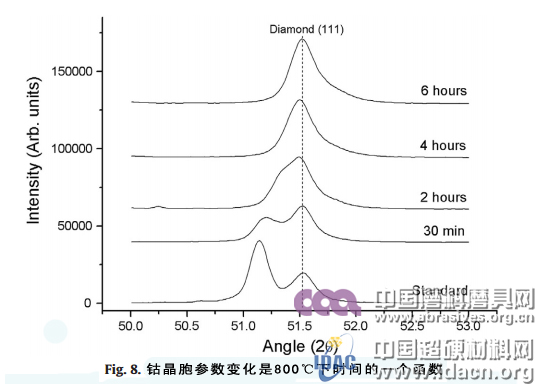
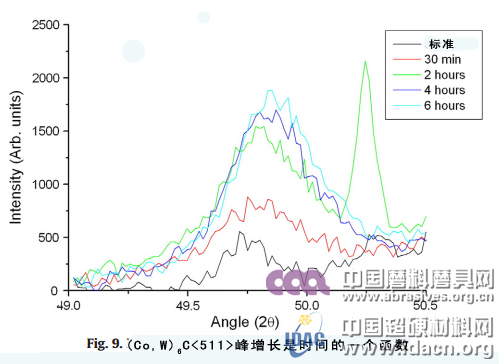
图10为750℃下加热2小时后TEM观测到的降解的钴坑。在钴-金刚石交界面有黑色颗粒。能谱定性分析显示该相有W,Co和C组成,沉淀钨含量要比周围钴坑要高许多。对黑色颗粒的电子衍射分析显示该相晶胞参数为a0=11.05±0.05 Å,拥有fcc晶体结构。这与X射线衍射分析中发现的(Co,W)6C相类似。
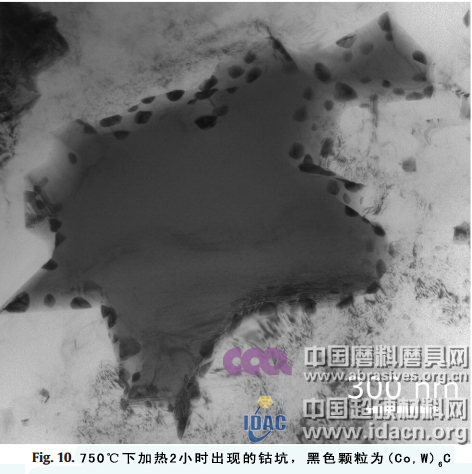
实验结合EELS利用HAADF-STEM来对试样进行石墨监测。图11为800℃下加热2小时的钴坑。在共生金刚石相(灰色区域)中可以观察到钴坑(明亮区域)。钴坑中的暗色区域经EELS分析为石墨。750℃加热2小时后没有发现任何金刚石转化为其他物质。图12a为标准材料的钴坑,在800℃下加热0.5小时后,观察到在钴中有石墨成核。12b为典型的成核图。随着时间和温度的增加,石墨坑的尺寸和数量密度大大增加。12c为 850℃下加热2小时的试样微结构。
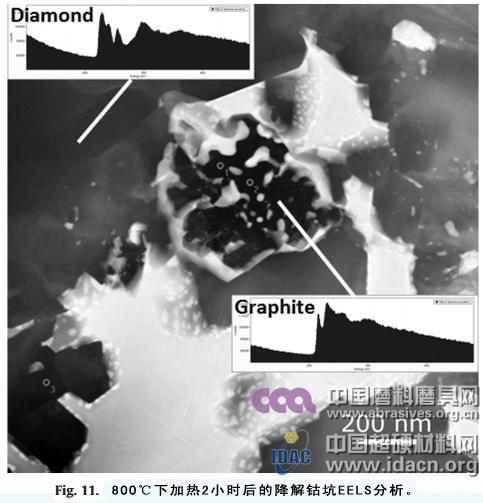
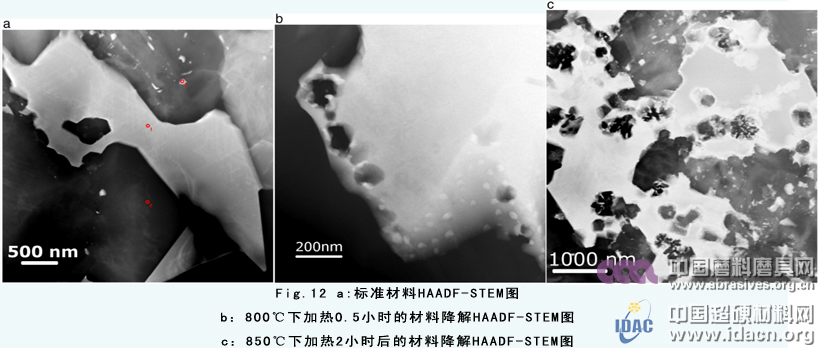
结论
如果将热机械测试试样的热降解状态与退火试样相比,研磨试验中工具接触面产生的温度要远远高于800℃。PCD材料上的裂纹主要是由材料上的各种力所致;金刚石结构内的裂纹主要是由工具和工件间的外力所致;而内力主要是由于金刚石-石墨转化时的体积膨胀以及金刚石和钴之间的不同热膨胀属性所致。固溶体钨和溶解碳反应生成的(Co,W)6C值得进一步研究,它可能会延迟石墨的生成。(翻译:中国磨料磨具网)