高温合金、特种陶瓷等高硬度热喷涂涂层的硬度一般在1000HV0.2以上,涂层厚度多在0.1mm—0.5mm之间,热喷涂层硬而薄。在磨削加工过程中,由于热喷涂层硬度高,多采用金刚石磨具加工。但由于采用金刚石固结磨—砂轮磨削不但有功率消耗大、磨削温度高、易烧伤工件、影响工件的表面和内在质量。而且还需要经常对砂轮进行修整,耗费工时。而使用普通磨料砂轮、砂带磨削加工,因其硬度低,其削效率更低或难磨(详见表一、各种物质的莫氏硬度表)。
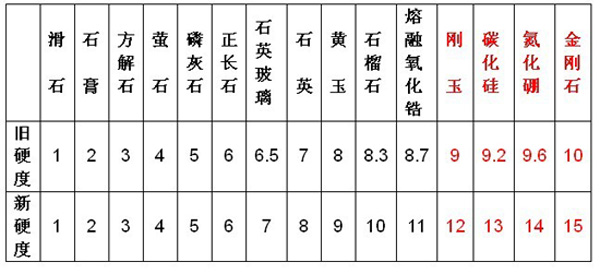
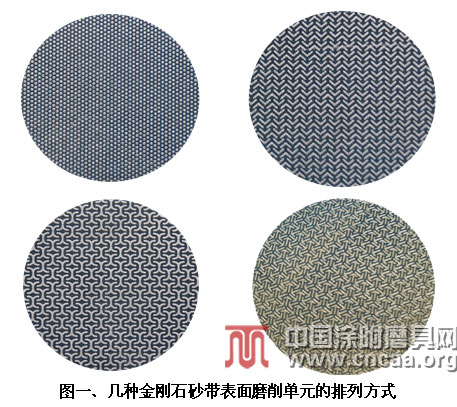
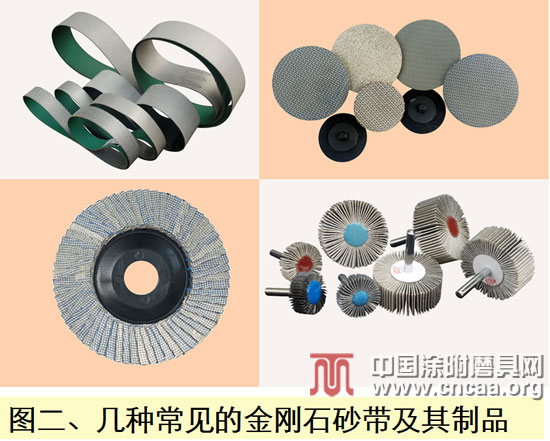
二、金刚石砂带磨加工方案与磨削工艺选择
金刚石砂带主要用于辊、轴类的加工,金刚石磨盘和金刚石叶轮主要用于平面、曲面及复杂型面的磨削与抛光。
(一)金刚石砂带磨加工热喷涂层方案
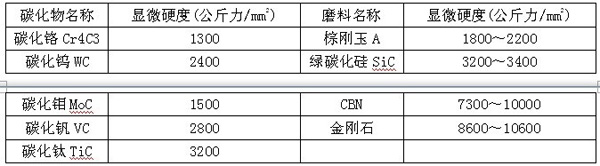
直径540mm×长度15m陶瓷活塞杆磨加工方案
直径540mm×长度陶瓷活塞杆磨加工工艺参数
车床型号:61125
砂带速度:16m/s (1500rpm)
砂带规格:60mm×1950mm
砂带接触工件方式:软接触(非接触轮磨)
工件规格:直径540mm×长度15m
工件转速:30rpm
磨头走刀速度:粗磨 60#、200# ,2mm—3mm/转;精磨 800# ,0.5mm—1mm/转
冷却液:水
工件喷涂材料:陶瓷涂层
喷涂涂层厚度:60μ
喷涂涂层的初始粗糙度:Ra0.4mm—0.6mm
喷涂涂层加工余量:25μ
加工后涂层厚度:35μ
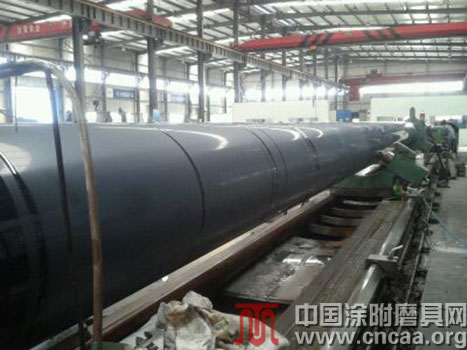
(二)金刚石砂带磨削工艺参数的选择
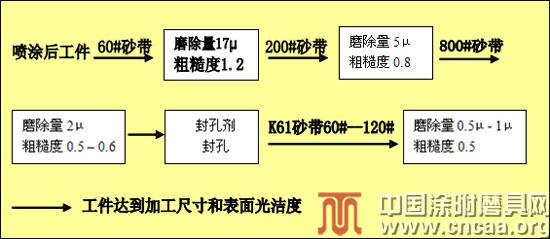
图四、金刚石砂带磨削加工工艺流程图
按照以上金刚石砂带磨削加工工艺(详见表二、金刚石砂带磨削工艺参数表),磨直径540mm×长度15m陶瓷活塞杆,其磨加工时间仅为90小时。而在第一次对其磨加工时,由于加工工艺设计不合理,磨加工时间则长达1个月之久。
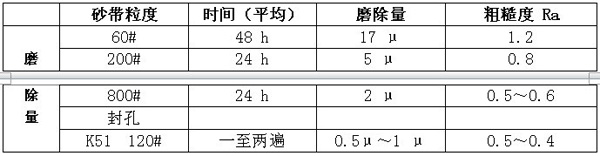
(三)金刚石砂带磨削加工方案的特点
1、优点:
(1)设备简单,操作方便,不需价格昂贵的专用磨床,可以装卡在常用规格的车床刀架上即可进行工作。
(2)磨抛速度快,效率高,磨削效果好。
(3)因为金刚石砂带表面金刚石颗粒的特殊有序排列设计,磨削锋利,排屑好,不需要修整。通过更换不同粒度的砂带即可达到加工要求。
2、缺点:
此类非接触轮磨削加工精度稍低(圆柱度方面),如果采用接触轮式磨抛(接触轮硬度90)即可在此基础上大大缩短加工时间并能达到工件的加工精度要求。
(四)决定加工的时间和质量因素:
1、喷涂涂层的质量:涂层厚度的均匀性及圆度,表面粗糙度的均匀性及表观质量,硬度的均匀性,涂层的气孔率,显微硬度的高低。
2、操作者的操作水平和操作习惯:如砂带磨头的进给压力等。
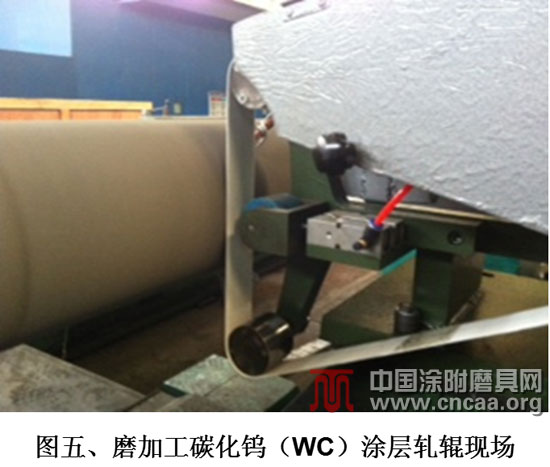
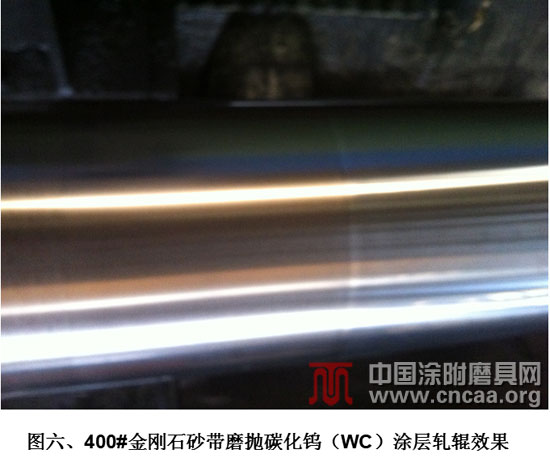
平面、曲面热喷涂层打磨方案
汽车冲压模具,汽轮机叶片以及航空部件等一些平面、曲面热喷涂后的打磨,目前比较先进的打磨方式是采用:
金刚石叶轮打磨平面和曲面:装在气动和电动磨机上,转速10000~20000rpm,打磨效率高,效果好,操作灵活方便。
金刚石磨盘打磨平面:装在气动和电动角磨机上使用,打磨速度快,光整性好。
金刚石转矩砂碟:规格直径2英寸,粒度200# 、400#装在高速气动工具,工具上,有小巧、操作灵活、装卸快速的特点。
金刚石叶轮,磨盘,转矩砂碟产品(见图二、几种常见的金刚石砂带及制品)打磨涂层的最大特点是:结构设计柔性,金刚石磨粒硬度高,磨削锋利,刚柔相兼,不会把涂层打透,且表面打磨均匀,一致性好。
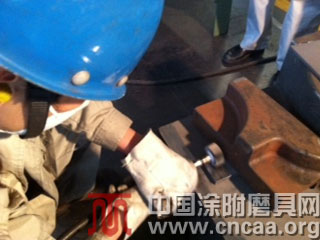
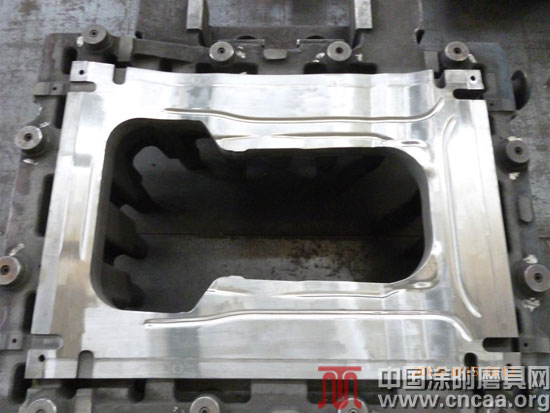
图八、经180目金刚石千叶轮抛光后,Ra 0.6-0.7
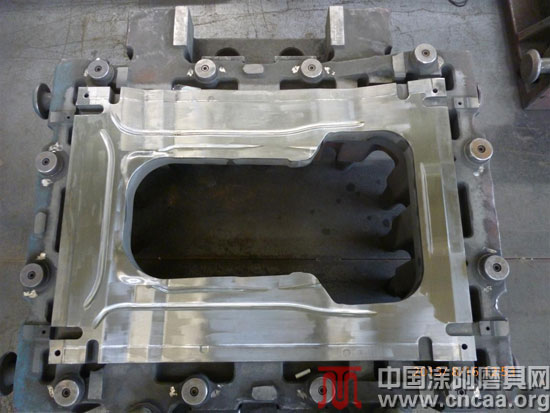
图九、经400目金刚石千叶轮抛光, Ra < 0.3
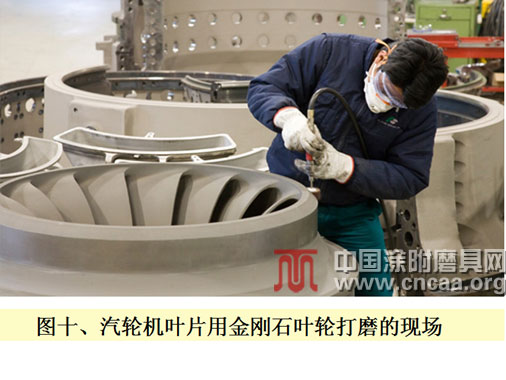
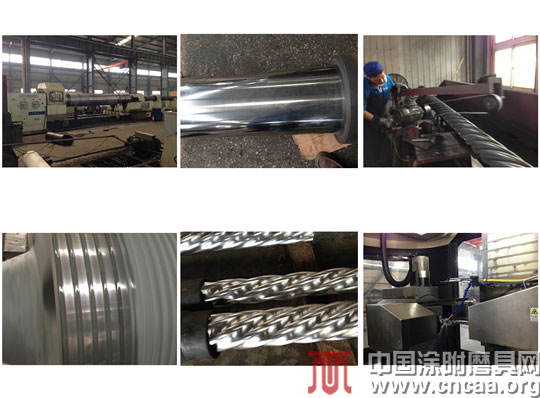
三、结语
目前,我国与先进国家相比,在热喷涂涂层的加工技术方面还是比较落后的,国内绝大多数工厂还是采用金刚石砂轮及金刚石薄膜振动抛磨的工艺,效率较低,采用金刚石砂带加工尚无相应的砂带机床与之配套,已成金刚石砂带磨削技术推广的瓶颈。我们已经开发成功与车床配套的砂带机,相信通过我们不懈的努力,一定会为我国热喷涂工业调整产业结构,创新发展做出自己的贡献。(作者: 郑州瑞特金刚石砂带有限公司 安建民)