机床型号为JUNKER (Jupiter500)无心磨床,结构见图1。无心磨床也称自定心磨床,由砂轮、导轮及托板与工件三点接触实现自动定心。工件磨削的质量与这几部分结构和调整都有着非常紧密的关系。
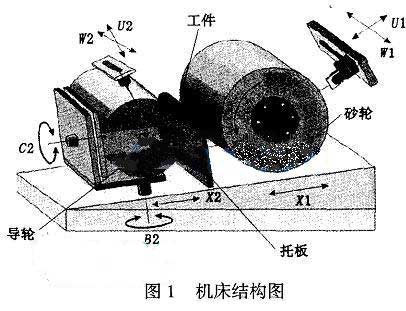
1.凸轮轴轴颈有锥度
这种情况主要是砂轮主轴和导轮主轴不平行所造成的,可通过调整C2和B2轴来实现,根据机床标尺直观可见。根据工件测量的结果来调整,然后进行锁定。
2.工件表面质量差
主要表现为棋盘纹路,表面粗糙度差,这种情况通常是由机床的振动造成的。首先,确保机床安装各紧固部位必须紧固到位,尤其是机床地脚螺栓必须锁紧。其次,检查砂轮动平衡装置是否可靠、设置是否合理。必要时休整砂轮和导轮并重新进行动平衡。
3.工件表面成不规则的多边形形状
工件在磨削时的稳定性非常关键,而无心磨床的稳定性主要是通过在磨削时工件受力平衡来保证,如图2所示。工件的稳定性主要取决于工件在导轮、砂轮、托架之间的高度H。H的数值取决于DP+D。和Db+D。的值,通过设备厂家线解图算得hl和h2值,一般情况H≈(hl+h2)/2,具体情况可根据实际进行微调。除了工件高度,砂轮也是一个主要的原因,砂轮的退出时间在初磨和精磨中是有区别的。在初磨中,砂轮在工件毛坯磨削成圆时退出,而在精磨时,砂轮接触到工件后即可退出,具体磨削效果可根据实际情况来微调。另外托架各档的高度是否一致也需要进行确认。
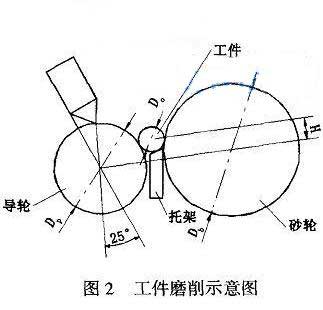
工件的表面成椭圆的原因很多,如果椭圆在每档中都出现的话,通常有一个规律,就是椭圆度在同一个相位角,这主要是砂轮进给不连续所造成的。砂轮进给不连续主要来源于两个方面,一是进给丝杠磨损有间隙,二是导轨润滑不良。如果椭圆出现在部分档位,且不固定,需要检查砂轮和导轮的表面是否修整完好以及是否粘有杂物。工件不定期出现圆度超差的现象,不确定在哪一个档位,通过检查砂轮和导轮,发现上面有铁屑,压入到砂轮或导轮中。由于有高点,磨削时就会出现上述现象,将工件清理干净再投入磨削,该现象消失。
5.工件表面有波纹痕迹
工件表面的波纹痕迹是由砂轮或导轮脱粒造成的,这时要检查确认砂轮和导轮选择是否合适或是否已经失效。一般需要考虑砂轮或导轮的粒度、硬度及粘结剂,同时和工件的磨削速度也有关,工件速度相对砂轮圆周速度的比例关系越大,砂轮应当越硬。为保证工件磨削表面质量,磨削液的过滤精度非常关键,通常过滤精度控制在5~l0μm。
二、曲轴外圆磨床
曲轴外圆磨床的工件缺陷如上所述,需要补充的是工件主轴和尾架的相关注意事项,主轴包括工件主轴和砂轮主轴,砂轮主轴动平衡很关键,其他精度都可以通过砂轮的修整来弥补。工件主轴的精度包括头架主轴间隙、端面跳动、主轴近端跳动、远端跳动、上母线和侧母线的精度以及和尾架的同轴度。图3、4、5、6为通常检验主轴精度的示意图。至于精度等级的要求视工件的精度要求而定。
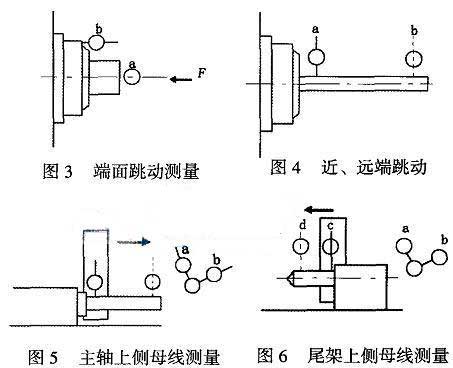
综上所述,磨床的常见缺陷主要和以下因素有关:机床本身(主轴、导轨、托架、尾架等)的静态几何精度是否丧失;工艺磨削参数是否合适;砂轮及其修整器是否存在缺陷和损坏;测量系统的误差;机床的动态精度及其砂轮的动平衡;切削液的过滤精度及其切削性能指标是否合适。