摘要 作者:L.Moro,A.Paul,D.C.Lorents,R.Malhotra,R.S.Ruoff摘要:热处理加工后,利用沉积200nm厚度的C60薄膜在(100)硅衬底上生
作者:L. Moro,A. Paul,D. C. Lorents,R. Malhotra,R. S. Ruoff
摘要:热处理加工后,利用沉积200nm厚度的C60薄膜在(100)硅衬底上生长出碳化硅薄膜。预沉积的C60在热处理过程中以及碳和硅反应生成碳化硅的过程中被严重破坏。反应开始于交界面,并伴随着硅逐渐融入已经形成的碳化硅中。低温(700℃)下,反应集中在交界面。硅扩散和理想配比的碳化硅的生成条件为800℃、100分钟以上热处理,900℃、25分钟以上热处理。理想配比薄膜的晶粒尺寸较为均匀,为20-40nm。求得900℃下碳化硅中硅的扩散系数为4×10-15cm2/s。由于硅在碳化硅薄膜的高渗透通道(如晶界和其他晶体缺陷等)中扩散的较快,当C60预沉积薄膜覆盖较大面积时,硅衬底上会产生凹陷和空隙等。
关键词:热处理,碳化硅,硅
1、引言
近年来,碳化硅材料凭借其优越的物理性能(宽带隙、高热导率、化学惰性、硬度和耐磨性)而广泛应用于微电子设备和微机电设备(MEMS)。不少研究者利用CVD法和分子束生长工艺在碳化硅或硅衬底上生长碳化硅薄膜。这些工艺要求1000℃-1500℃的高温加工条件,高温制备的条件将碳化硅薄膜的制备限制在了能承受高温的制造设备上。
本实验利用C60和Si及SiO2的不同反应,在硅衬底上采用C60碳化的方法低温(80-1000℃)制备外延β-SiC。实验主要研究硅衬底上从预沉积C60薄膜开始生长的碳化硅薄膜情况,详细观察碳化硅薄膜的生长情况和薄膜质量。
2、实验方法
衬底材料为(100)硅晶片,利用有机溶剂对其进行油污处理,并用去离子水进行清洗。晶片表面污渍采用RCA洗涤液(H2O2:NH4OH:H2O, 1:1:4 ;80 °C)清洗10分钟;利用HF溶液对其表面的氧化物进行去除,时间低于1分钟,然后用去离子水进行清洗。最后将衬底晶片放置在高真空炉内数分钟。
在高真空炉内(P=10-7 Torr)的硅晶片上沉积出200-300nm厚的C60薄膜。然后将其切割成1×1cm2的硅片,分别放置在超高真空炉内(P<10-8 Torr)进行热处理。为防止热处理过程中蒸发导致的C60损耗,将每两片衬底相对而放,把C60限制在两个硅片中间。热处理温度为700℃、800℃和900℃,处理时间为5、25、100、150和300分钟。
利用激光电离(SALI)质谱法对热处理工艺生成的C60分解进行测量。采用355nm的纳秒Nd:YAG激光器进行材料的激光解吸;采用118nm辐射的皮秒Nd:YAG激光器进行定位。
利用俄歇电子显微镜(AES)对碳化硅的形成进行观察,并根据Si和C的谱线形状进行深度剖析。AES测量采用PHI4200薄膜分析仪,工作压力低于2×10-10 Torr. 实验还用到装配了共轴电子枪的筒镜分析器。本研究所用电子束电压和电流为3keV和280nA。仪器分辨率设定为0.6%。所有试样都在同一实验条件下进行分析。利用Ar+离子枪对所有试样进行溅射处理,每隔30-60秒进行数据获取。
摘要:热处理加工后,利用沉积200nm厚度的C60薄膜在(100)硅衬底上生长出碳化硅薄膜。预沉积的C60在热处理过程中以及碳和硅反应生成碳化硅的过程中被严重破坏。反应开始于交界面,并伴随着硅逐渐融入已经形成的碳化硅中。低温(700℃)下,反应集中在交界面。硅扩散和理想配比的碳化硅的生成条件为800℃、100分钟以上热处理,900℃、25分钟以上热处理。理想配比薄膜的晶粒尺寸较为均匀,为20-40nm。求得900℃下碳化硅中硅的扩散系数为4×10-15cm2/s。由于硅在碳化硅薄膜的高渗透通道(如晶界和其他晶体缺陷等)中扩散的较快,当C60预沉积薄膜覆盖较大面积时,硅衬底上会产生凹陷和空隙等。
关键词:热处理,碳化硅,硅
1、引言
近年来,碳化硅材料凭借其优越的物理性能(宽带隙、高热导率、化学惰性、硬度和耐磨性)而广泛应用于微电子设备和微机电设备(MEMS)。不少研究者利用CVD法和分子束生长工艺在碳化硅或硅衬底上生长碳化硅薄膜。这些工艺要求1000℃-1500℃的高温加工条件,高温制备的条件将碳化硅薄膜的制备限制在了能承受高温的制造设备上。
本实验利用C60和Si及SiO2的不同反应,在硅衬底上采用C60碳化的方法低温(80-1000℃)制备外延β-SiC。实验主要研究硅衬底上从预沉积C60薄膜开始生长的碳化硅薄膜情况,详细观察碳化硅薄膜的生长情况和薄膜质量。
2、实验方法
衬底材料为(100)硅晶片,利用有机溶剂对其进行油污处理,并用去离子水进行清洗。晶片表面污渍采用RCA洗涤液(H2O2:NH4OH:H2O, 1:1:4 ;80 °C)清洗10分钟;利用HF溶液对其表面的氧化物进行去除,时间低于1分钟,然后用去离子水进行清洗。最后将衬底晶片放置在高真空炉内数分钟。
在高真空炉内(P=10-7 Torr)的硅晶片上沉积出200-300nm厚的C60薄膜。然后将其切割成1×1cm2的硅片,分别放置在超高真空炉内(P<10-8 Torr)进行热处理。为防止热处理过程中蒸发导致的C60损耗,将每两片衬底相对而放,把C60限制在两个硅片中间。热处理温度为700℃、800℃和900℃,处理时间为5、25、100、150和300分钟。
利用激光电离(SALI)质谱法对热处理工艺生成的C60分解进行测量。采用355nm的纳秒Nd:YAG激光器进行材料的激光解吸;采用118nm辐射的皮秒Nd:YAG激光器进行定位。
利用俄歇电子显微镜(AES)对碳化硅的形成进行观察,并根据Si和C的谱线形状进行深度剖析。AES测量采用PHI4200薄膜分析仪,工作压力低于2×10-10 Torr. 实验还用到装配了共轴电子枪的筒镜分析器。本研究所用电子束电压和电流为3keV和280nA。仪器分辨率设定为0.6%。所有试样都在同一实验条件下进行分析。利用Ar+离子枪对所有试样进行溅射处理,每隔30-60秒进行数据获取。
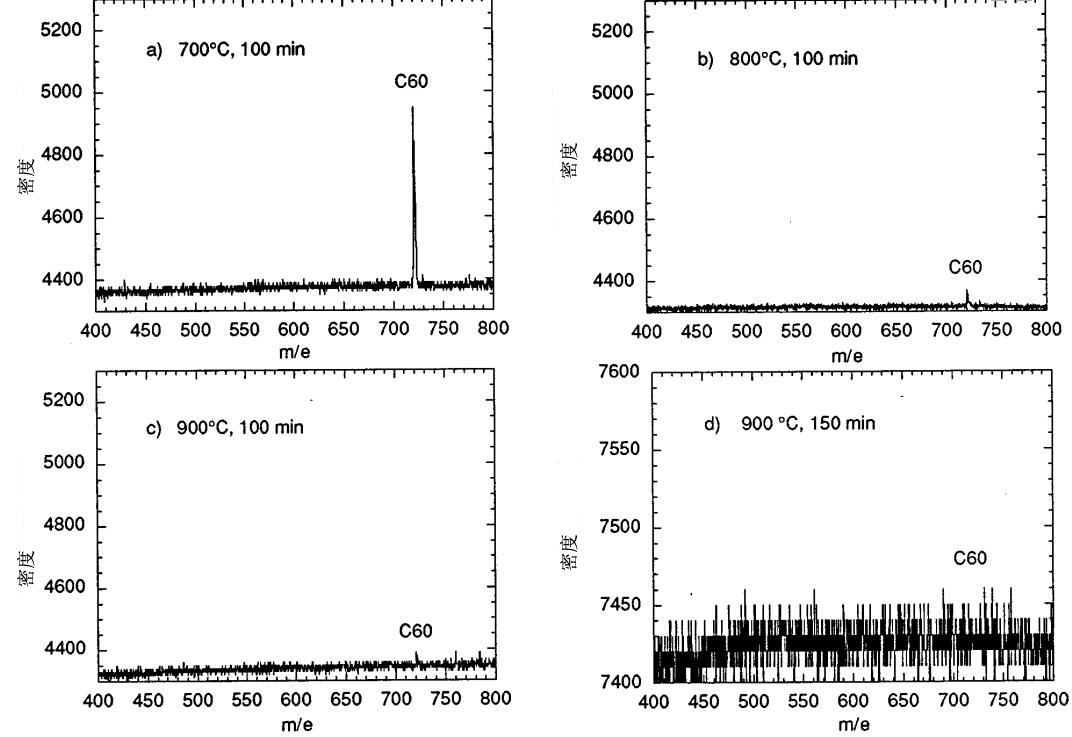
图一:700℃、800℃和900℃条件下热处理100分钟后的SALI质谱:C60峰值逐渐变得不再强烈。900℃下热处理150分钟后,峰值彻底消失
为获得较好的深度分辨率并研究交界面上碳化硅的形成,实验借助Ar等离子INA3设备对试样进行了二次深度分辨率质谱分析。为优化深度剖析的深度分辨率和敏感度,溅射能量设定为700eV。利用Dektak触针表面光度仪对试样上的沟痕深度进行测量,以此求得碳化硅的溅射速率。然后利用该溅射率将其他所有时标转化为深度。在此过程中,假定溅射条件保持不变。
利用SEM对薄膜形态进行观察,用装配有传统钨丝的JEOL6100设备检测二次电子信号,工作电压25kV。利用JEOL2000FX TEM获取每一个试样的TEM图和电子衍射,工作电压200keV。TEM试样可以通过对硅衬底的清除可得(HF:HNO2:乙酸=3:5:3),利用TEM网格对漂浮在溶液上的透明碳化硅薄膜进行收集。
3、结果
利用SALI检测C60薄膜和硅的反应,并测量C60峰值在试样表面的强度。图1为恒定时间段内(100分钟)三个热处理温度条件下(700℃、800℃和900℃)试样的SALI光谱。图中还显示了900℃下热处理150分钟的试样光谱。随着热处理时间的增长和温度的提高,C60信号逐渐减弱,在900℃,时间大于100分钟时已经观察不到最原始的C60。在热处理过程中,C60薄膜和硅发生反应,很快被消耗并生成碳化硅。
图2为代表性试样的俄歇深度剖面,揭示了整个过程的动态变化情况。(a)是700℃下热处理100分钟的试样图。在此条件下,界面上没有观察到硅;而800℃和100分钟的条件下也没有观察到硅。而在(b)中,800℃加热150分钟时,硅在C60薄膜中扩散并发生反应,最终生成碳化硅。
利用SEM对薄膜形态进行观察,用装配有传统钨丝的JEOL6100设备检测二次电子信号,工作电压25kV。利用JEOL2000FX TEM获取每一个试样的TEM图和电子衍射,工作电压200keV。TEM试样可以通过对硅衬底的清除可得(HF:HNO2:乙酸=3:5:3),利用TEM网格对漂浮在溶液上的透明碳化硅薄膜进行收集。
3、结果
利用SALI检测C60薄膜和硅的反应,并测量C60峰值在试样表面的强度。图1为恒定时间段内(100分钟)三个热处理温度条件下(700℃、800℃和900℃)试样的SALI光谱。图中还显示了900℃下热处理150分钟的试样光谱。随着热处理时间的增长和温度的提高,C60信号逐渐减弱,在900℃,时间大于100分钟时已经观察不到最原始的C60。在热处理过程中,C60薄膜和硅发生反应,很快被消耗并生成碳化硅。
图2为代表性试样的俄歇深度剖面,揭示了整个过程的动态变化情况。(a)是700℃下热处理100分钟的试样图。在此条件下,界面上没有观察到硅;而800℃和100分钟的条件下也没有观察到硅。而在(b)中,800℃加热150分钟时,硅在C60薄膜中扩散并发生反应,最终生成碳化硅。
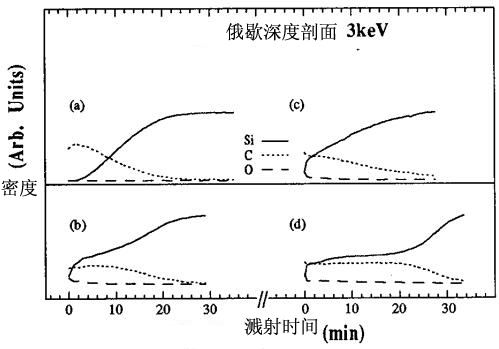
图二:不同热处理条件下的俄歇深度剖面:(a)700℃,100分钟;(b)800℃,150分钟;(c)900℃,5分钟;(d)900℃,150分钟
图2(c)为试样在900℃下热处理5分钟的剖面图。此时,表面可以观察到硅信号,但硅和碳的谱线形状分析表明没有反应发生。但在同样的热处理温度下,延长时间后(如图d所示),开始发生反应。试样在900℃下热处理25分钟后也会发生同样的反应(该数据图中未给出)。这些数据都明确说明碳化硅的行程手硅扩散的影响控制,而硅的扩散有取决于热处理温度和时间的联合作用。
根据碳和硅的谱线形状由石墨碳、结晶硅到典型的碳化物形态的演变,我们利用AES对碳化硅的行程进行检测。结果表明,碳化硅在800℃下热处理时间超过100分钟后开始形成;而在900℃下热处理时间为25分钟时就可是反应生成。900℃下热处理超过25分钟后,得到理想配比的碳化硅,如图2定量AES深度剖面图所示。
图3为两个试样在900℃条件下分别热处理5分钟和150分钟的硅LVV和C KLL导数光谱。为进行对比,还对批量的外延附生碳化硅的谱线形状进行研究。将信号强度校对至各自对应的峰间值高度。图3(b)中,谱线形状由石墨碳(实线;900℃,5分钟)到碳化物(点线;900℃,150分钟)的变化很明显。碳化物和标准样品(密集虚线,点-短划线;取向附生碳化硅)的相似度非常明显。图3(a)中可以观察到所有硅谱线形状的硅-碳键合。
根据碳和硅的谱线形状由石墨碳、结晶硅到典型的碳化物形态的演变,我们利用AES对碳化硅的行程进行检测。结果表明,碳化硅在800℃下热处理时间超过100分钟后开始形成;而在900℃下热处理时间为25分钟时就可是反应生成。900℃下热处理超过25分钟后,得到理想配比的碳化硅,如图2定量AES深度剖面图所示。
图3为两个试样在900℃条件下分别热处理5分钟和150分钟的硅LVV和C KLL导数光谱。为进行对比,还对批量的外延附生碳化硅的谱线形状进行研究。将信号强度校对至各自对应的峰间值高度。图3(b)中,谱线形状由石墨碳(实线;900℃,5分钟)到碳化物(点线;900℃,150分钟)的变化很明显。碳化物和标准样品(密集虚线,点-短划线;取向附生碳化硅)的相似度非常明显。图3(a)中可以观察到所有硅谱线形状的硅-碳键合。
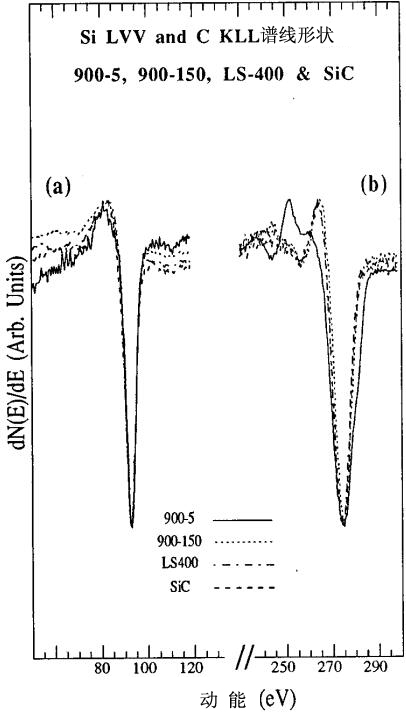
图三:(a)不同试样的硅LVV和C KLL谱线形状对比示意图
为研究碳化物的反应是否是从交界面开始,我们使用SNMS深度轮廓仪对比了硅衬底和热处理后的C60薄膜之间的界面宽度。由于C60和硅相互反应,低温条件下(700℃)进行了热处理之后,交界面变宽。SNMS轮廓仪揭示了硅在碳薄膜中的扩散。在700℃下,反应主要集中在交界面上;随着热处理温度的提高和时间的延长,C60薄膜上的反应继续进行。
对于800℃和900℃条件下热处理的试样,可以利用实验部分的SNMS方法对其进行碳化硅生长层厚度的测量。上述结果如图4所示。
对于800℃和900℃条件下热处理的试样,可以利用实验部分的SNMS方法对其进行碳化硅生长层厚度的测量。上述结果如图4所示。
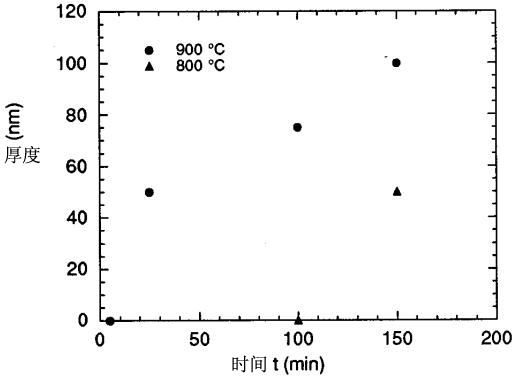
图四:碳化硅薄膜层的厚度和热处理时间的函数关系(900℃,方形;800℃,三角形)
SEM形态观测表明:热处理实验条件下可以生成连续均匀的薄膜(如图5所示,900℃,150分钟),带有一些生长缺陷(空隙和凸起丘堆);这和硅在生长出的碳化硅薄膜中扩散的路径一致。对于低温短时间条件下生长出的薄膜,其横向、纵向均匀性不是很好,同时还形成了多孔的碳化硅区域(图中未显示)。根据次级离子质谱分析法,我们推断这可能和硅表面区域残留的自然氧化物有关。这些氧化区掩盖了碳化硅的成核作用并促使附近的碳化硅颗粒横向生长。
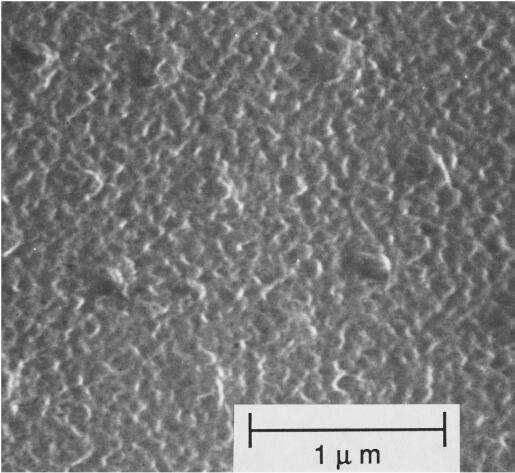
图五:900℃下热处理150分钟后制备而成的碳化硅薄膜SEM图。薄膜上的空隙缺陷对应着衬底上的凹陷,凸起丘堆对应着由于硅供给的增多而导致的生长速率增强区
研究利用TEM对薄膜的晶粒尺寸和结晶度进行测量。利用蚀刻的方法从衬底上得到的Si-C材料(800℃热处理100分钟;900℃热处理150分钟的试样)有黑色布状材料构成。图6为800℃条件下热处理100分钟的试样TEM图。与之相对,900℃下热处理150分钟的试样则产生了非常透明、直立式大片薄膜。
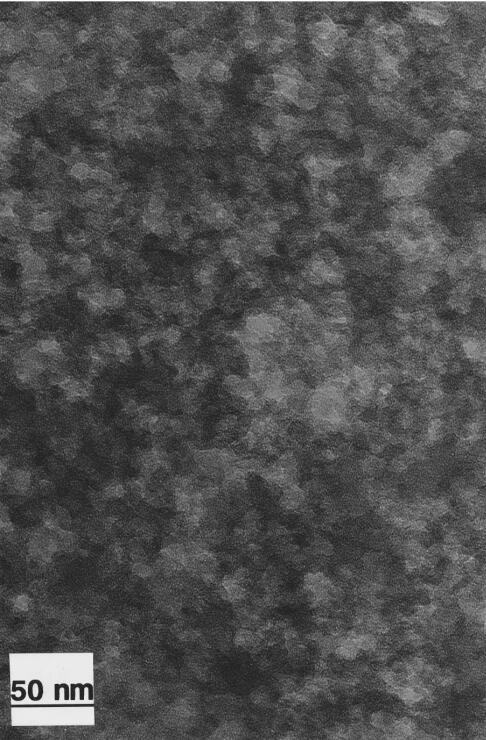
图六:800℃下热处理100分钟的薄膜TEM图(E=200keV,放大率=150000);图中有局部发生反应的碳和无定形碳化硅
图七为试样的TEM图。晶粒尺寸在20-40nm。晶粒堆中还有一些尚未反应转化的碳,和其他晶粒相比,呈暗黑色。一些晶粒的结晶缺陷也较为明显(孪晶、位移等)。根据电子衍射图分析得到的晶格参数便是碳化硅的性能特征,弹药区分α-碳化硅和β-碳化硅的类型则不太可能。
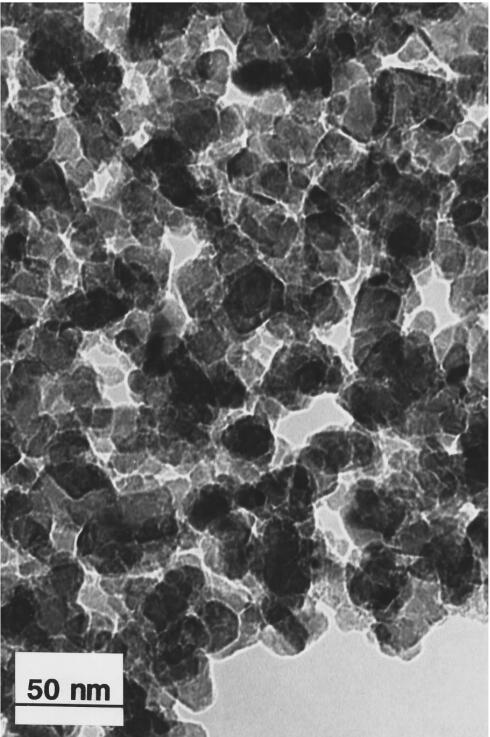
图七:900℃下热处理150分钟的薄膜TEM图(E=200keV,放大率=150000)。图中有未反应的碳晶粒和晶体缺陷(孪晶和位移等)
4、讨论
利用C60分子和(100)、(110)硅的反应制备碳化硅在之前的研究中已经提到过。但本研究提出了一种替代方案,即利用预沉积薄膜在硅衬底上生长碳化硅薄膜。该方法的一个难点在于如何将表面上的C60热处理温度限制在足够高的范围内(T>800℃)以便于C60和硅能继续发生反应。我们采用两片衬底相对放置的方法,建立一个高效的C60超压装置。
在热处理过程中通过沉积出包覆层可以实现对C60的限制。在我们之前的一个研究中,就提到了“离子改性”C60包覆层的方法。利用包覆层将C60限制在选定区域内可以更加直接快捷地在硅衬底上模仿碳化硅的结构。这要比Hamza等人提出的根据C60束在硅衬底和二氧化硅表面的不同反应的方法更具优势。
根据对700℃以上热处理试样进行深度剖面分析,预沉积C60薄膜和衬底的扩散界面证实了C60和硅的反应发生在C60层和硅衬底之间的界面上。在相同温度范围内,Hamza等人则得出Si(100)衬底上碳化硅的形成必须持续暴露在C60的供给流中。碳化硅晶粒的成核作用在热处理早期发展的很快。
在经过初期的成核阶段之后,碳化硅层的生长速度逐渐变缓(图2)。在热处理时间和温度方面,800℃且超过100分钟、900℃且超过25分钟的热处理工艺制备出明显厚度的碳化硅薄膜。
根据图8的数据可以估算出900℃下硅在碳化硅中的扩散速度为4.8×10-15cm2/s。由于厚度计算和可用实验点较少的缘故,该值在相对较大的试验误差内为常量。而Hamza及其同事估算出的数值则为7.7×10-15cm2/s。据此我们可以估算扩散过程中的活化能为1.17eV。
5、结论
本实验证明了在900℃热处理条件下可以利用硅衬底上C60薄膜的预沉积来制备同质化碳化硅薄膜。当C60预沉积薄膜覆盖较大面积时,用于反应的硅在已经形成的的碳化硅薄膜中扩散,并优先扩散到薄膜缺陷区。在硅衬底上,这些有限扩散路径产生了凹陷。下一步,本实验将继续研究碳化硅薄膜的机械和电子性能。(编译:中国磨料磨具网)
利用C60分子和(100)、(110)硅的反应制备碳化硅在之前的研究中已经提到过。但本研究提出了一种替代方案,即利用预沉积薄膜在硅衬底上生长碳化硅薄膜。该方法的一个难点在于如何将表面上的C60热处理温度限制在足够高的范围内(T>800℃)以便于C60和硅能继续发生反应。我们采用两片衬底相对放置的方法,建立一个高效的C60超压装置。
在热处理过程中通过沉积出包覆层可以实现对C60的限制。在我们之前的一个研究中,就提到了“离子改性”C60包覆层的方法。利用包覆层将C60限制在选定区域内可以更加直接快捷地在硅衬底上模仿碳化硅的结构。这要比Hamza等人提出的根据C60束在硅衬底和二氧化硅表面的不同反应的方法更具优势。
根据对700℃以上热处理试样进行深度剖面分析,预沉积C60薄膜和衬底的扩散界面证实了C60和硅的反应发生在C60层和硅衬底之间的界面上。在相同温度范围内,Hamza等人则得出Si(100)衬底上碳化硅的形成必须持续暴露在C60的供给流中。碳化硅晶粒的成核作用在热处理早期发展的很快。
在经过初期的成核阶段之后,碳化硅层的生长速度逐渐变缓(图2)。在热处理时间和温度方面,800℃且超过100分钟、900℃且超过25分钟的热处理工艺制备出明显厚度的碳化硅薄膜。
根据图8的数据可以估算出900℃下硅在碳化硅中的扩散速度为4.8×10-15cm2/s。由于厚度计算和可用实验点较少的缘故,该值在相对较大的试验误差内为常量。而Hamza及其同事估算出的数值则为7.7×10-15cm2/s。据此我们可以估算扩散过程中的活化能为1.17eV。
5、结论
本实验证明了在900℃热处理条件下可以利用硅衬底上C60薄膜的预沉积来制备同质化碳化硅薄膜。当C60预沉积薄膜覆盖较大面积时,用于反应的硅在已经形成的的碳化硅薄膜中扩散,并优先扩散到薄膜缺陷区。在硅衬底上,这些有限扩散路径产生了凹陷。下一步,本实验将继续研究碳化硅薄膜的机械和电子性能。(编译:中国磨料磨具网)