聚合物及其混合物在摩擦设备中的广泛应用使得诸多学者对聚合物复合材料的摩擦性能进行了研究分析。机械载荷和磨损率决定了聚合物复合材料在设备中的可适性。磨损可以定义为固体表面材料的损耗,是由接触表面的相对运动所致。磨损的五种主要类型为磨料磨损、粘着磨损、微振磨损、腐蚀磨损和疲劳磨损;其中磨料磨损是五种磨损形式中最为常见也是最重要的一种磨损,占整个磨损类型的63 %。
聚合物复合材料的磨料磨损常见发生在土方工程设备、管道、凿岩、矿石破碎机等设备中。该材料强度高、硬度大、耐磨性好、能够根据材料中纤维和基体组份的调整来改变材料性能。常用于轴承、凸轮、砂轮、叶轮、闸、离合器、传动带和齿轮等设备,并收到摩擦载荷作用影响,从而是磨损更加严重。而基体中加入填料则增加了载荷承受容量,降低摩擦系数,改善耐磨性能和热性能。此外,填料还能降低复合物复合材料的耗费成本。
2.实验
2.1材料
基体材料为LAPOXL-12级的环氧树脂和K-6室温固化剂。按照一定的重量百分比将环氧树脂、花岗岩和碳化硅填料混合。环氧树脂重量百分比不变,通过改变碳化硅填料和花岗岩填料的比例,制备出三种不同组份的复合材料。
2.2三体磨损试验
根据ASTM G-65在干砂轮/橡胶砂轮磨损试验机上进行三体磨损试验。在旋转橡胶砂轮和试样接触面处进行磨料进给。试验中旋转速度为200 rpm。磨料进给为235±5 g/min。通过失重计算磨损,磨损率(Ks)计算公式如下:
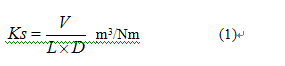
V是容量损失(m3),L为载荷(N),D为磨削距离(m)。
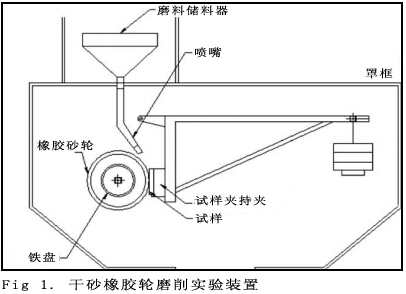
2.3实验设计
本研究利用田口法实验设计(DOE)。DOE是在不同因子准级下做实验并同时对多个因子的影响效果进行分析研究。因子是一个对输出结果有直接影响的变量或参数。准级是对因子数值的设置;如表一所示:
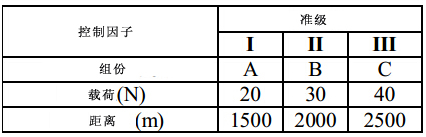
本研究采用L9阵列设计。试验观察结果转化为S/N比。
3.结果和讨论
整个实验有9组测试3个因子,如表二所示。利用田口法对实验结果进行分析;影响磨损的显著参数如表三所示。
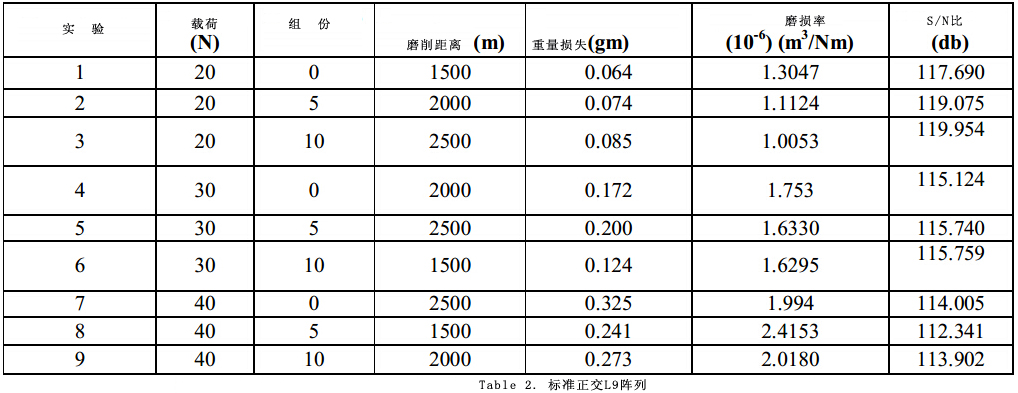

3.1主效应和交互作用图
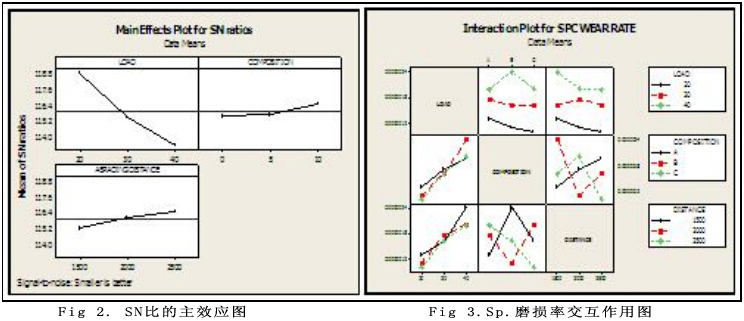
图二为minitab-15软件产生的主效应图,显示了三个控制因子及其准级对复合材料试样的磨损率的影响。当一个因子的不同准级分别影响响应时,就可以观察到一个主效应。当线条为水平时,没有主效应;线条倾斜时出现主效应。直线越陡峭,主效应对磨损率的量级就越大。最小磨损率出现在20N载荷、1500m距离处。
当一个因子的效应依赖另一个因子的准级时,可以用交互作用图来显示其交互作用;图中的平行线则表示没有交互。线条间斜率差越大,交互程度也就越大。从图三的交互作用图可以看出,磨削距离和组份之间的交互作用对磨损率的影响最大。
3.2 变量分析
ANOVA分析的结果如表四所示。表格最后一列为每个因子对复合材料磨损率的影响比例。
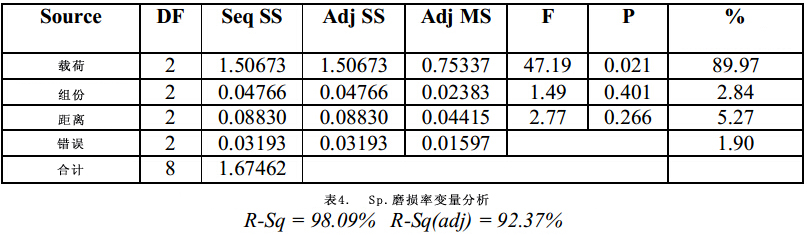
从表中可以看出,载荷对复合材料磨损率的影响最大,占89.97 %;其次是磨削距离,占5.27 %;组份占据比例最小,为2.84 %。相关的合并误差约1.90 %。
3.3载荷、磨削距离和组份对具体磨损率的影响
图四可以看出,磨损率随磨削距离增大而减小,随载荷增大而增大。与其他两种组份相比,10 wt%碳化硅填料的G-E复合材料的磨损率相对较低;这是由于材料中填料分布均匀,基体和填料的粘合性较好。
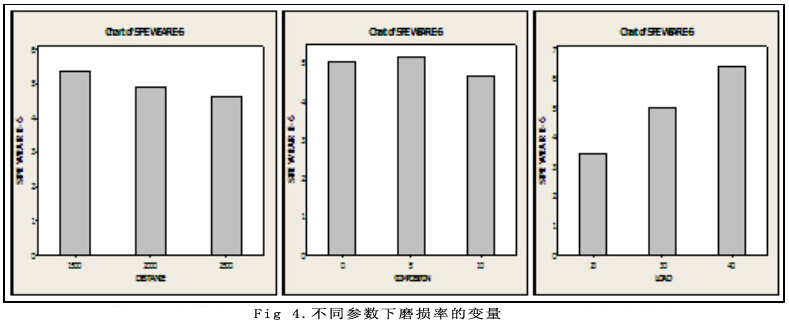
3.4磨损表面形态
为更好的关联磨损数据,在不同载荷下拍摄磨削试样的SEM照片。图五、六、七分别为G-E材料和碳化硅填料G-E材料磨损表面的SEM特征图,载荷为20N和40N。图五中,G-E材料表面富含树脂层,空隙和碎屑都比较少。树脂层很好的改善了粘结性能和表面整体性。G-E材料的磨料磨损要比GE-SiC材料的磨损严重,这是由于没有碳化硅填料的G-E材料基体较软,受磨削力影响大,硬质磨料和软基体相互接触摩擦引起基体损坏。
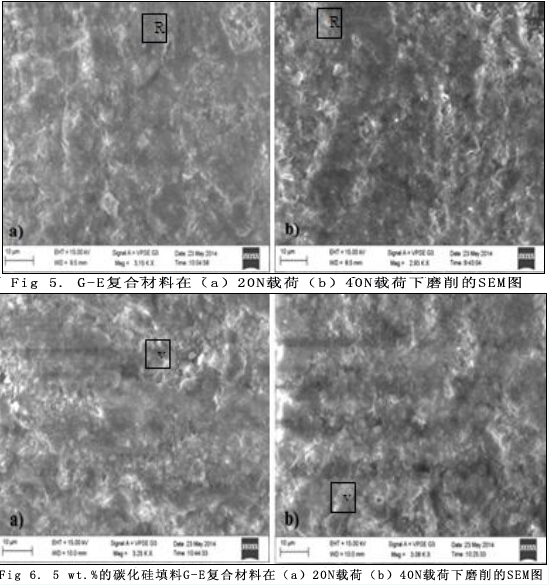
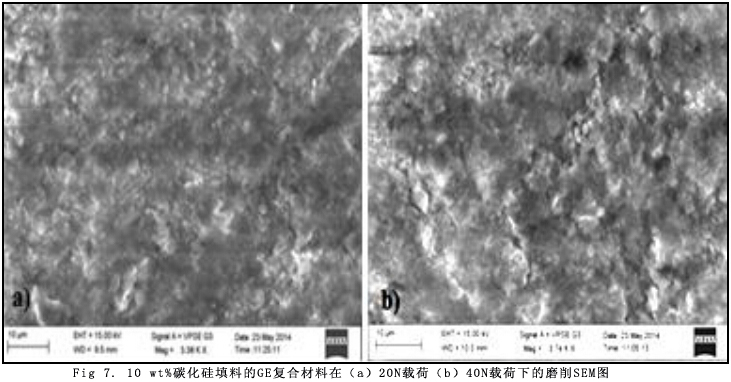
图六中5%碳化硅填料的G-E材料显示出颗粒状断裂特征和较浅深度的表面波纹,这是由硬质碳化硅颗粒和柔软的环氧树脂基体结合带来的脆性所致。基体表面光滑,局部区域出现空白,这是由于磨削距离和载荷增大导致精细磨料破碎所致。
图七中10%碳化硅填料的G-E材料显示出颗粒状断裂特征和深度更加浅的表面波纹,这说明由硬质碳化硅颗粒和柔软的环氧树脂基体结合带来的脆性更加明显。
4.结论
磨损率随载荷增大而增大;随磨削距离增大而降低。10%碳化硅填料的G-E材料耐磨性能要比其他两个类型的材料要好。
根据ANOVA分析,载荷对耐磨性影响最大,占89.97 %;磨削距离对其影响占5.27 %,其次是材料组份,占2.84 %。
G-E复合材料的磨损表面说明出现了严重的基体损坏;而碳化硅填料GE材料的表面磨损则比较轻微,这是由于碳化硅硬质颗粒相存在的缘故。