摘要 对A12O3和PTC陶瓷薄件进行了固着磨料研磨实验,分析了不同参数对磨削效率和表面粗糙度的影响,提出了有效研磨工程陶瓷薄件的方法。
主题词 工程陶瓷 切除率 表面粗糙度
在前一研究中,作者曾进行了用游离磨料研磨PTC半导体陶瓷(Ti2O3)和A12O3陶瓷薄件的实验研究[1]。结果表明,在游离磨料研磨加工中,对于表面形貌为脆性断裂凹坑或其与塑性沟痕的组合,研磨工艺参数和研磨盘材料对加工效果有明显的影响,可以获得高的平面度和较好的表面质量,但是加工效率低,陶瓷薄件易破碎,成品率低。树脂结合剂研磨片具有一定的弹性,金属结合剂研磨片具有良好的磨削性能和耐磨性。固结磨料研磨片作用于工件表面的力均匀,可以减少工件的破碎;多个研磨片组成的砂轮,可以提高研磨效率和表面质量,小直径研磨片在研磨液的冲洗下,不易堵塞;工件的平面度可以通过研磨片的及时修整得到保证。通过研磨片组成的砂轮和被研磨工件间的不规则运动,可实现工程陶瓷薄件高质量的平面加工。
本文采用不同的金刚石、碳化硅树脂研磨片,以及金刚石金属结合剂研磨片,进行了PTC半导体陶瓷和Al2O3工程陶瓷的研磨工艺研究。针对某PTC半导体陶瓷加工厂的实际需求,力图优选出一种适用于生产应用的研磨片成份和使用工艺,替代目前的游离磨料研磨工艺。
1 实验
实验使用一台改装后的游星轮单面研磨机,工件放置在一个可转动的圆盘上。为避免工件相互撞击,用粘结剂将工件粘在磨盘表面,研磨片则粘在一个可自转的游星轮的压块上,通过在压块上增加负重来调节研磨压力。圆盘转动时,游星轮自转。用精密测微仪器测量工件和研磨片研磨高度的微小变化,并计算磨削比,测量研磨前后的表面粗糙度。在扫描电镜上观察了研磨片和工件的表面形貌。图1为加工实验装置示意图。以PTC为主要研究对象,氧化铝作为对比。氧化铝和PTC的显微硬度值分别为1507.44HV0.1。和623.9HV0.1。试件厚度为2/mm。研磨转速为50、100、150、200r/m,实测行星轮自转速度为80r/m,抛光盘直径为380/mm。磨削压力为13、17、22、26、31 N。研磨液为水和实测浓度为0.5%的一种非离子表面活性剂为主的水溶性冷却液。
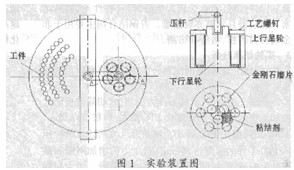
所用研磨片直径为10mm,厚度为2mm,实验用研磨片按结合剂—磨料—粒度—浓度进行标识,分别为PI—RVD—270/325—75%。PI—RVD—W28—75%,PF—RVD—W28—75%,PI—RVD—W14—75%,PI—SiC—W14—100%,633Cu—RVD—W28—100%。树脂研磨片洛氏硬度(67.5kg,1/8)为90~95。
2 研磨片制造及其本性能
PF树脂磨片以热塑性酚醛树脂为结合剂的主要原料,添加适宜的固化剂(乌洛托品),再添加一定量的填料如Cr2O3、Cu、CeO、SiC磨粒等与金刚石RVD微粉一起充分混合,在模具内冷压成型,然后采用合适的升温曲线固化成型而成,目前在超硬磨料磨具中采用树脂结合剂所占的比例约超过半数。
PI树脂磨片是采用聚酰亚胺树脂为结合剂的主要原料。其特点是自聚合成型不需另加固化剂,连续使用温度高,在空气中可在300℃温度下使用,而酚醛是170℃左右。
树脂结合剂研磨片磨削时自锐性好,不易堵塞,一般情况下一次修整后就不需再修整,磨削效率高,磨削力小,磨削温度低,同时结合剂本身还具有一定的弹性和抛光性能,工件被加工表面光洁度高,表面质量好。主要用于要求磨削效率和加工光洁度较高的场合。树脂结合剂的缺点是耐磨性差,磨具的磨损较大,不适合大负荷磨削。树脂片成型工艺流程:原材料准备—混合过筛—模压—后固化。
青铜结合剂研磨片是以铜粉、锡粉和铅粉等为结合剂主要材料,采用液体石蜡为润湿剂,与磨料充分混合后压制成型,再在还原气氛下烧结而成。青铜结合剂结合强度高,耐磨性好,磨损小,磨具的使用寿命长,形状保持性好,能承受较大负荷,但自锐性差,容易堵塞、发热,磨具修整亦较困难。青铜结合剂主要用于非金属材料的粗、精磨和切割。
3 实验结果分析
3.1研磨压力、研磨时间和研磨转速与研磨效果的关系
从图2可以看出,随着压力的增加,切除量也随之增加。由于Al2O3的硬度比m要大,磨粒难以切人,Al2O3,切除量比PTC要小。随着压力的增加,磨粒压入PTC工件的深度达到一定值,压力的增加对断裂破碎的影响减弱,切除量的增加速度也减慢。压力对粗糙度的影响不显著,但是表面粗糙度略有上升。这表明在实验压力范围内,磨粒与工件之间均以脆性断裂为主。磨削压力越大,脆性凹坑越多,但磨粒和结合剂与工件之间的接触面积越大,使得结合剂的磨抛作用加强,表面粗糙度变化不大。
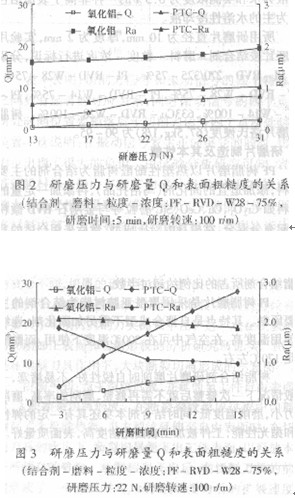
从图3可知,随着研磨时间的增长,研磨量直线上升,工件表面粗糙度呈下降趋势,并逐渐平稳。研磨PTC约9分钟时,接近工件在这种磨粒粒度作用下所能达到的最小粗糙度值。磨粒粒度对研磨表面质量起最主要的作用。同游离磨粒研磨结果一样,研磨转速越高、磨粒越粗,切除量越大,表面粗糙度越低。而变化幅度与研磨片磨粒种类、结合剂种类和工件材料等有关(图4、图5)。
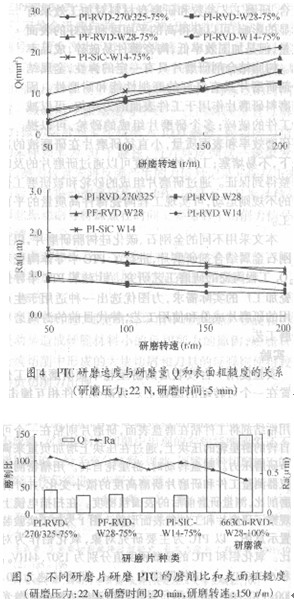
3.2研磨片磨粒粒度、磨粒种类和结合剂对m研磨效果的影响
磨粒种类:比较PI—SiC—W14—100%和PI—RVD—W14—75%可以看出,SiC研磨片的磨削效率、磨削比与金刚石树脂研磨片差别不大,磨粒脱落是磨损的主要形式,但表面粗糙度很差。研磨转速高时,研磨量之间的差别减小,但对Ra的影响较小。
磨粒粒度:磨粒越粗,研磨切除量越大,表面粗糙度越低。对研磨量和磨削比来说,PI—RVD—270/325—75%和PI—RVD—W14—75%间的差异,大于PI—RVD—W28—75%和PI—RVD—W14—75%间的差异,表明磨料粒度越粗,对研磨量的影响程度越大,这一差异与研磨转速关系不大。对表面粗糙度而言,PI—RVD—270/325—75%和PI—RVD—W28—75%间的差异,随研磨转速的提高而减小;PI—RVD—W28—75%和PI—RVD—W14—75%间的差异,受研磨转速影响不大。这可以大致说明,随磨粒粒度变大Ra由快速下降转为较慢变化。在PI—RVD—W14—75%表面表现出明显的塑性变形沟痕和平坦的表面(图6a)。
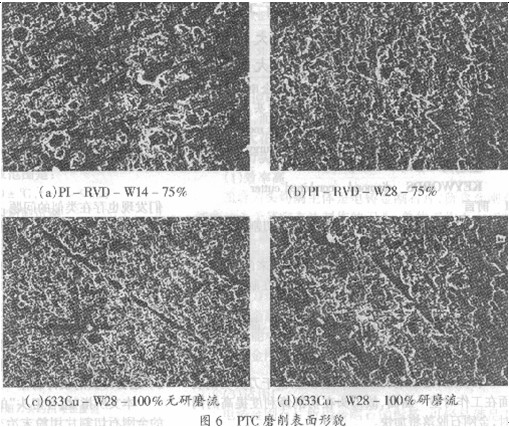
结合剂种类:从图4,5可知,相同条件下,PF结合剂的研磨片研磨量、磨削比要比PI结合剂的研磨片高,但表面粗糙度低,随着转速的增高,研磨量的差距更明显。由图可见,青铜结合剂金刚石研磨片的磨削比远高于树脂结合剂研磨片,在采用了一种研磨液后,研磨性能进一步提高。PF结合剂研磨片上的金刚石脱落量明显少于PI研磨片,PTC研磨表面Ra值也最小。
在实验条件下,实际观察到的PTC表面形貌表明,PI—RVD—W14—75%磨削表面质量高于青铜结合剂表面质量,磨粒粒度对表面粗糙度的影响最大。青铜结合剂金刚石研磨片表面金刚石自锐性良好,并未产生堵塞。从提高磨削效率来考虑,对于PTC加工而言,选用金属结合剂金刚石精磨片可获得最佳磨削比和表面质量。若再采用细粒度金刚石,可使表面质量得到进一步提高。
3.3工件材料对研磨效果的影响
对比图4、图7可以看出,在相同的实验研磨工艺条件下,不同的材料可研磨性也不同。PTC切除量比A12O3大,表面粗糙度低,这与使用游离磨料的加工结论是相同的。
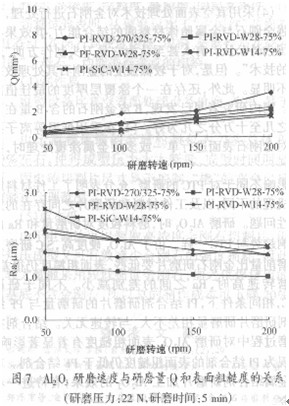
不同的磨料种类、结合剂种类对Al2O3研磨效果的影响不同于对PTC的研磨,充分表明了工件材料磨削机理的不同,以及工件材料和研磨片之间存在的适应性问题。研磨她03时,磨料粒度对研磨量和Ra的影响趋势与唧一样。由于A12O3硬度高,SiC研磨片的磨削量比金刚石研磨片要低些,表面粗糙度仍很差。
研磨转速高时,Ra之间的差别减小。不同于研磨PTC,相同条件下,PI结合剂研磨片的研磨量与PF结合剂研磨片研磨量相差不大,与转速无关。结合剂在研磨过程中对研磨A12 O3表面粗糙度有着显著影响,表现为PI结合剂的表面粗糙度仍低于PF结合剂。对于金属结合剂研磨片加工鸽03的效果,有待进一步研究。
4结论
1)影响研磨效率和研磨质量的因素主要有磨粒粒度、结合剂种类、磨料种类、研磨转速、研磨压力和研磨液成分。对于不同的工件材料,上述因素的影响效率不同。
2) 对于眦半导体陶瓷片加工,应采用金属结合剂研磨片加上研磨液来进行高效研磨工。合适的研磨片成分、减少研磨片尺寸、合理排列研磨片和添加研磨液可改善研磨片的自锐性。采用细粒度树脂结合剂金刚石研磨片则可进一步提高加工表面质量。
参考文献
1 袁慧等.工程陶瓷游离磨料研磨加工工艺研究.机械工艺师(待发表)
2 人造金刚石合成与金刚石工具的制造.中南工业大学出版社
3 刘忠等.工程陶瓷磨削形成机理及磨削类型.天津大学学报,1993(4)
4 吴忠琪等.工程陶瓷锐面加工研磨与抛光技术.天津大学学报,1996(2)
5 江晓乐等.氧化铝工程陶瓷的磨料加工技术.磨床与磨削,1993(1)